Электродуговая сварка магистральных и промысловных трубопроводов
2.1. Подготовка к сборочным и сварочным работам
2.1.1. Аттестацию электросварщиков перед допуском их к сварке трубопроводов или перед допуском к специальным работам следует осуществлять в соответствии с "Положением об аттестации электросварщиков", утвержденным Миннефтегазстроем (справочное приложение I).
2.1.2. Операционный контроль сварки следует осуществлять в соответствии со СНиП III-42-80 и операционными технологическими картами.
2.1.3. Квалификационные испытания электросварщиков проводятся в соответствии с п.4.16 СНиП III-42-80.
2.1.4. В процессе проверки квалификации сварщика по п.4.16 СНиП III-42-80 сварка допускных стыков в зависимости от изменения марки стали и сварочных материалов назначается в соответствии с таблицами 1 и 2 при изменении групп трубных сталей и групп сварочных материалов.
Таблица 1
Номер группы | Нормативное значение временного сопротивления разрыву трубной стали, МПа |
I | 330 - 410 включительно |
II | Свыше 411 до 539 включительно |
III | Свыше 539 до 588 включительно, кроме труб термического упрочнения |
IV | Свыше 539 до 588 включительно для труб термического упрочнения |
V | 637 для труб термического упрочнения |
Таблица 2
Номер группы | Тип, класс прочности | Металлургический вид покрытия электрода, флюса, порошковой проволоки | Марки электродов, проволок, сочетания флюс + проволока, проволока + защитный газ |
1 | 2 | 3 | 4 |
1 | Э42-Э50 | Ц Целлюлозный | ВСЦ-4, Фокс Цель, Кобе-6010, Кобе-7010, Пайпвелд-6010, Пайпвелд-7010 |
2 | Э60 | Ц " | ВСЦ-60, Кобе-8010 |
3 | Э42А | Б Основной | УОНИ-13/45 |
4 | Э50А | Б " | УОНИ-13/55, Фокс ЕВ 50, ЛБ-52У, ЛБ-52А, Феникс К50Р, ОК.48.04 |
5 | Э50А | Б " | ВСО-50СК (для сварки "на спуск") |
6 | Э60 | Б " | ВСФ-65У, Шварц-ЗК, Кессель-5520М0, ЛБ-62Д, ЛБ-58У, ОК.73.79 |
7 | Э70 | Б " | ВСФ-75У, ЛБ-65Д, ОК.74.78 |
8 | ПС44 | Б " | ПП-АН19 |
9 | ПС44 | Б Основной | ПП-АН24СМ |
10 | ПС49 | Б " | ПП-АН30С |
11 | К50 | Кислый | АН-348А + СВ-08 АН-348А + СВ-08А АН-348А + СВ-08АА |
12 | К55 | " | АН-348 + СВ-08ГА (АН-348АМ + СВ-08ГА) |
13 | К55 | Среднеосновной | АН-47 + СВ-08 АН-47+ СВ-08А АН-47+ СВ-08АА АН-47+ СВ-08ГА |
14 | К55-К60 | " | АН-47 + СВ-08ХМ АН-47 + СВ-08МХ |
15 | К55-К60 | Слабоосновной | АН-ВС + СВ-08ХМ АН-ВС + СВ-08МХ АН-ВС + СВ-08ХГ2СНМТ |
16 | К60-К65 | " | ФЦ-16 + СВ-08ГНМ |
17 | К55 | - | СВ-08ГС, СВ-08Г2С, Ar + СО ; СО |
18 | К55-К60 | - | СВ-08ГС, СВ-08Г2С, Ar + СО ; СО |
19 | К60-К65 | - | СВ-08Г2С, СВ-08Г2СМ, Ar + СО ; СО |
Примечание. Если сварщик сварил допускной стык одной маркой или сочетанием марок сварочных материалов, входящих в соответствующую группу, он квалифицируется на сварку всеми сварочными материалами (или их сочетанием), входящими в данную группу.
2.1.5. Рекомендуемые типы разделки кромок труб приведены на рис.1.
Рис.1. Типы разделки кромок труб для ручной дуговой сварки, односторонней автоматической сварки под флюсом, автоматической дуговой сварки порошковой проволокой с принудительным формированием, полуавтоматической сварки в защитных газах:
а - для труб диаметром 57-1420 мм с толщиной стенки до 16 мм;
б - для труб диаметром 273-1420 мм с толщиной стенки более 15 мм; в - для автоматической сварки труб в защитных газах
Примечания: 1. После газовой резки в монтажных условиях разделка кромок труб должна соответствовать рис.1,а независимо от толщины стенки труб.
2. Размер (мм) на рис.1,б зависит от толщины стенки трубы (мм):
мм | Толщина стенки трубы, мм |
7 | Свыше 15 до 19 |
8 | Свыше 19 до 21,5 |
10 | Свыше 21,5 до 26 |
12 | Свыше 26 до 32 |
3. Если изменятся формы заводской разделки кромок (см. рис.1,а,б), для последующей двусторонней автоматической сварки под флюсом или в защитных газах эта операция должна быть выполнена механическим способом непосредственно перед сваркой.
2.1.6. Эквивалент углерода металла низкоуглеродистых низколегированных сталей независимо от состояния их поставки - горячекатаные, нормализованные и термически упрочненные - определяется по формулам, указанным в п.13.11 СНиП 2.05.06-85.
2.1.7. Сварку допускного стыка разрешается выполнять бригадным методом. В этом случае каждый сварщик бригады получает право выполнять сварку только того слоя шва, который был им сварен на допускном стыке.
В случае изменения состава бригады к работе в этой бригаде может быть допущен сварщик, получивший ранее право сварки данного слоя или всего шва.
2.1.8. Требования к выполнению и качеству допускных стыков должны соответствовать СНиП III-42-80 и ВСН 012-88 (см. справочное приложение 2).
2.1.9. При испытании образцов на изгиб в соответствии с п.4.19 СНиП III-42-80 диаметр нагружающей оправки выбирается в соответствии с табл.3.
Таблица 3
Состояние трубной стали | Временное сопротивление разрыву, МПа | Вид испытания на изгиб | Диаметр нагружающей оправки (см. ГОСТ 6996-66), мм |
1 | 2 | 3 | 4 |
Горячекатаная, нормализованная | До 490 | Корнем шва внутрь или наружу | 2 ±2 ( - толщина стенки трубы) |
| | На ребро | 30 ±2 |
Нормализованная, контролируемая прокатка | Более 490 до 539 | Корнем шва внутрь или наружу | 3 ±2 |
| | На ребро | 40 ±2 |
Нормализованная, термически упрочненная, контролируемая прокатка | От 539 до 637 | Корнем шва внутрь или наружу | 4 ±2 |
| | На ребро | 50 ±2 |
2.1.10. При отсутствии деталей заводского изготовления допускается изготовление отводов, тройников и тройниковых соединений в условиях, тождественных заводским; при этом необходимо соблюдать требования СНиП 2.05.06-85.
2.1.11. Материал деталей трубопроводов должен обеспечивать свариваемость с металлом труб. Типоразмеры деталей трубопроводов заводского изготовления определяются проектной документацией.
Запрещается использовать арматуру из серого или ковкого чугуна.
2.1.12. Для сварки могут быть использованы трубы и детали трубопроводов, дефекты на поверхности которых не превышают по размеру допусков, регламентированных ГОСТами, ТУ на поставку труб и деталей трубопроводов.
2.1.13. Забоины и задиры фасок глубиной до 5 мм ремонтируют с применением электродов с основным видом покрытия, выбираемых в соответствии с табл.10, и подогревом, рекомендуемым при сварке данных труб.
2.2. Сборка стыков труб перед сваркой
2.2.1. Перед сборкой необходим визуальный контроль поверхностей труб, деталей трубопроводов, запорной и распределительной арматуры в соответствии с требованиями п.4.1 СНиП III-42-80; обнаруженные дефекты должны быть исправлены в соответствии с требованиями п.4.2 СНиП III-42-80.
2.2.2. Соединение разностенных труб, труб с деталями трубопроводов или труб с запорной и распределительной арматурой должно выполняться в соответствии с п.4.5 СНиП III-42-80.
Примечание. Допускается выполнять непосредственную сборку и сварку труб с деталями трубопроводов при разностенности до 2,0 толщин при специальной подготовке детали (рис.2).
Рис.2. Подготовка для сварки торцов труб с разной толщиной ( ) стенки.
2.2.3. При сборке стыков труб с одинаковой нормативной толщиной стенки должны соблюдаться следующие требования:
внутреннее смещение внутренних кромок бесшовных труб не должно превышать 2 мм. Допускаются на длине не более 100 мм местные внутренние смещения кромок труб, не превышающие 3 мм;
величина наружного смещения в этом случае не нормируется, однако, должен быть обеспечен плавный переход поверхности шва к основному металлу в соответствии с технологической картой. Оценку величины смещения внутренних кромок следует проверять непосредственным измерением с использованием шаблонов марки УПС-4;
смещение кромок электросварных труб не должно превышать 20% нормативной толщины стенки, но не более 3 мм. Измерение величины смещения кромок допускается проводить по наружным поверхностям труб сварочным шаблоном. Для труб с нормативной толщиной стенки до 10 мм допускается смещение кромок до 40% нормативной толщины стенки, но не более 2 мм. В случае необходимости следует делать селекцию и калибровку (см. справочное приложение 3).
2.2.4. Сборку труб следует производить в соответствии с п.4.3 СНиП III-42-80. Для сборки труб диаметром 1420 мм с толщиной стенки 21,5 мм и выше следует применять внутренние центраторы ЦВ-145 с повышенным усилием разжатия 1960-2250 кН. До начала серийного выпуска таких центраторов можно пользоваться центратором ЦВ-144 усовершенствованной конструкции.
Сборку захлестов, а также других стыков, где применение внутренних центраторов невозможно, разрешается производить с помощью наружных центраторов независимо от диаметра труб, в том числе гидравлических.
2.2.5. Способы сборки промысловых трубопроводов под ручную и автоматическую дуговую сварку под флюсом изложены в ВСН 005-88.
2.2.6. Величины зазоров в стыках при сборке в случае сварки электродами приведены в табл.4.
Таблица 4
Способ сварки | Диаметр электрода или сварочной проволоки, мм | Величина зазора при толщине стенки трубы, мм |
| | до 8 | 8-10 | 10 и более |
Ручная дуговая сварка электродами с основным покрытием | 2,0-2,5 | 1,5-2,5 | - | - |
| 3,0-3,25 | 2,0-3,0 | 2,5-3,5 | 3,0-3,5 |
Ручная дуговая сварка электродами с целлюлозным покрытием | 3,0-3,25 | 1,5-2,0 | - | - |
| 4,0 | - | 1,5-2,5 | 1,5-2,5 |
Ручная дуговая сварка электродами с рутиловым покрытием | 2,0-2,5 | 1,5-2,5 | - | - |
| 3,0-3,25 | 2,0-3,0 | 2,5-3,5 | 3,0-3,5 |
Примечание. Величину зазора при сварке способом "на спуск" электродами с основным покрытием следует устанавливать по максимальному значению.
2.2.7. Сборку стыков при двусторонней автоматической сварке под флюсом следует выполнять без зазора. На отдельных участках стыка длиной до 100 мм допускается зазор не более 0,8 -1,0 мм.
2.2.8. Величина зазора при сборке стыков на трубосварочных базах ССТ-ПАУ зависит от способа и технологии выполнения подварочного слоя:
если подварку изнутри трубы выполняют вручную, то ее следует осуществлять сразу после сварки корня шва; при этом стыки собирают с зазором, рекомендованным для ручной дуговой сварки электродами с основным покрытием;
если подварку изнутри трубы выполняют автоматической сваркой под флюсом, то сборку стыка следует выполнять с зазором не менее 1,5 мм.
2.2.9. Сборку стыков при автоматической сварке в защитных газах производят без зазора. Допускаются локальные зазоры до 0,5 мм.
2.2.10. Сборку под двустороннюю автоматическую сварку выполняют с помощью одной прихватки, расположенной в соответствии с рис.3 на режимах сварки первого наружного слоя шва. Длина прихватки должна быть не менее 200 мм.
Рис.3. Расположение прихваток при сборке под двустороннюю автоматическую сварку под флюсом:
1 - положение сварочной головки в начале сварки;
2 - прихватка
2.2.11. При сборке стыков на наружных центраторах количество прихваток, равномерно распределенных по периметру стыка, и их длина зависят от диаметра трубы и должны соответствовать данным, приведенным в табл.5.
Таблица 5
Диаметр стыка, мм | Ориентировочное количество прихваток, не менее | Длина прихваток, не менее, мм |
До 400 | 2 | 30-50 |
400 - 1000 | 3 | 60-100 |
1000 - 1400 | 4 | 100-200 |
2.2.12. Непосредственно перед прихваткой и сваркой производится просушка (или подогрев) кольцевыми нагревателями торцов труб и прилегающих к ним участков шириной не менее 150 мм.
2.2.13. Просушка торцов труб нагревом до температуры 20-50°С обязательна:
при наличии влаги на трубах независимо от способа сварки и прочности основного металла;
при температуре окружающего воздуха ниже +5°С в случае сварки труб с нормативным временным сопротивлением разрыву 539 МПа (55 кгс/мм ) и выше.
2.2.14. Предварительный подогрев выполняют перед прихваткой и ручной дуговой сваркой корневого слоя шва. Необходимость подогрева и его параметры определяют по табл. 6 и 7 в зависимости от эквивалента углерода стали, толщины стенок стыкуемых труб, температуры окружающего воздуха, вида покрытия электродов.
Примечание. Требования таблиц не распространяются на термоупрочненные стали.
2.2.15. Если по условиям пп.2.2.13-2.2.14 необходимы и просушка, и подогрев, то обязательной является только последняя операция.
2.2.16. При сварке корневого слоя шва термически упрочненных труб с нормативным пределом прочности 637 МПа (65 кгс/мм ) электродами с целлюлозным видом покрытия независимо от температуры окружающего воздуха необходим предварительный подогрев стыка до температуры не ниже +100°С, но не выше +200°С.
При сварке корневого слоя шва электродами с основным видом покрытия при температуре окружающего воздуха +5°С и ниже температура кромок труб стыка непосредственно перед сваркой должна быть не ниже +50°С, но не более +200°С.
2.2.17. Предварительный подогрев при сварке стыков труб на трубосварочных базах следует применять только непосредственно перед прихваткой и ручной дуговой сваркой корневого слоя шва на базах типа ССТ-ПАУ и БНС.
2.2.18. Перед автоматической сваркой под флюсом заполняющих слоев шва на базах типа ССТ-ПАУ, а также при двусторонней автоматической сварке под флюсом кольцевых стыков труб на базах типа БТС предварительный подогрев не требуется.
Таблица 6
Температура предварительного подогрева при сварке корневого слоя шва электродами с целлюлозным видом покрытия
Таблица 7
Температура предварительного подогрева при сварке корневого слоя шва электродами с основным видом покрытия
2.2.19. Температуру предварительного подогрева перед сваркой труб из различных марок сталей или разностенных труб, каждая из которых должна быть подогрета на различную температуру, устанавливают по ее максимальному значению.
2.2.20. Параметры предварительного подогрева при полуавтоматической сварке в углекислом газе определяют по табл.7, регламентирующей подогрев при сварке корневого шва электродами с основным видом покрытия.
2.2.21. Температуру подогрева свариваемых кромок нужно контролировать контактными термометрами (например, ТП-1, ТП-2 или термокарандашами).
Замерять температуру следует на расстоянии 10-15 мм от торца трубы; место замера необходимо предварительно зачистить металлической щеткой.
2.2.22. Если при замере температуры непосредственно перед сваркой будет обнаружено, что температура стыка оказалась ниже установленной в табл. 6 и 7, то необходим повторный нагрев.
2.3. Сварочные материалы
2.3.1. Для сварки кольцевых стыков магистральных и промысловых трубопроводов разрешено применять следующие виды сварочных материалов, предусмотренные проектом и прошедшие приемку и оценку качества перед их применением согласно требованиям приложения 4:
электроды с целлюлозным видом покрытия (Ц) для ручной дуговой сварки неповоротных стыков или с основным видом покрытия (Б) для ручной дуговой сварки поворотных и неповоротных стыков*;
флюс и сварочную проволоку для автоматической сварки под флюсом поворотных стыков труб;
самозащитную порошковую проволоку для автоматической и механизированной сварки неповоротных стыков труб с принудительным формированием шва;
защитный газ и сварочную проволоку для автоматической и полуавтоматической сварки в защитных газах.
* Для отдельных категорий промысловых трубопроводов разрешаются электроды с рутиловым (Р) покрытием (см. ВСН 005-88).
Применение сварочных материалов без сертификата завода-изготовителя запрещается.
2.3.2. Сварочные материалы должны соответствовать требованиям проекта, в котором могут быть предусмотрены следующие нормативные документы:
ГОСТ 9466-75 "Электроды покрытые металлические для ручной дуговой сварки сталей и наплавки. Классификация, размеры и общие технические требования";
ГОСТ 9087-81 "Флюсы сварочные плавленые";
ГОСТ 2246-70 "Проволока стальнан сварочная";
ТУ 14-1-4171-86 "Сварочная проволока марки Св-08ХГ2СНМТ";
ТУ 14-146-73-87 "Флюс сварочный плавленый двухсоставной марки АН-ВС";
ГОСТ 10157-79 "Аргон газообразный";
ГОСТ 8050-85 "Двуокись углерода газообразная и жидкая";
ТУ 1-1768-76 "Сварочная проволока Св-08Г2СМ";
ТУ 14-4-1172-82 "Порошковая проволока ПП-АН19";
ТУ 88 УССР 085-348-83 "Порошковая проволока ПП-АН24С";
ТУ ИЭС 514-85 "Порошковая проволока ПП-АН-30".
2.3.3. Сварочные материалы (электроды и порошковую проволоку) следует хранить преимущественно в отапливаемых помещениях при температуре не ниже +15°С в условиях, предохраняющих от загрязнения, увлажнения, ржавления и механических повреждений.
2.3.4. Электроды и порошковую проволоку следует хранить в упаковке завода-изготовителя на стеллажах или в штабеле. Высота укладки упаковок не должна превышать 5 рядов.
2.3.5. Мотки (бухты, катушки) проволоки сплошного сечения необходимо хранить на складе в упаковке завода-изготовителя. Приемка мотков (бухт, шпуль, катушек) проволоки должна быть осуществлена только при наличии металлической бирки с указанием наименования товарного знака предприятия-изготовителя, условного обозначения проволоки, номера плавки и партии.
2.3.6. Флюсы необходимо хранить в бумажных мешках, уложенных в штабель, или в специальных закрытых емкостях (контейнерах, бункерах, ларях). В случае повреждения упаковки флюсы следует хранить только в контейнерах, бункерах, ларях.
2.3.7. Порошковая проволока должна быть уложена в герметизированную жестяную банку отдельными мотками массой 10 кг и не более 35 кг. Банки с проволокой должны храниться на стеллажах. К мотку должна быть привязана бирка, на которой указывают марку порошковой проволоки, номер партии, дату изготовления. Мотки должны быть упакованы в мешки из полиэтиленовой пленки. В каждый полиэтиленовый мешок должен быть уложен матерчатый мешок с прокаленным селикагелем в количестве 0,5% от массы проволоки.
2.3.8. Сварочные электроды, флюсы, порошковую проволоку непосредственно перед их выдачей в производство необходимо сушить (прокаливать) согласно режимам, приведенным в табл.8.
Таблица 8
Тип и марка сварочных материалов | Температура прокалки, °С | Время выдержки, ч |
Электроды: | | |
Э42, Э50 | 60-100 | 1,0 |
Э42А | 250 | 1,0 |
Э50А | 300 | 1,0 |
Э60, Э70 | 350 | 1,0 |
Флюсы: | | |
АН-348А | 200-300 | 1,5 |
АН-47 | 300-350 | 1,5 |
АН-ВС | 300-350 | 1,5 |
ФЦ-16 | 400-500 | 3,0-3,5 |
Порошковая проволока: | | |
ПП-АН19 | 230-250 | 2,0-3,0 |
ПП-АН24СМ | 200-230 | 1,5-2,0 |
ПП-АН30С | 200-230 | 1,5-2,0 |
Примечание. Электроды с целлюлозным покрытием, доставленные к месту работ с неповрежденной герметической упаковкой (жестяных банках или картонных коробках с герметизирующей пленкой), разрешается использовать по назначению без предварительной сушки.
2.3.9. Электроды, флюсы и порошковая проволока используются после сушки (прокалки) в сроки, указанные в табл.9. Дальнейшее их применение разрешается только после проведения повторной сушки (прокалки).
Таблица 9
Сварочные материалы | Срок годности при хранении в сухих помещениях, сут |
Электроды с основным видом покрытия и порошковая проволока | 2 |
Электроды с целлюлозным видом покрытия | 5 |
Флюс | 15 |
2.3.10. При температуре окружающего воздуха ниже +5°С прокаленные электроды, предназначенные для сварки корневого слоя шва с основным видом покрытия непосредственно после сушки (прокалки), рекомендуется термостатировать в специальных электротермопеналах типа ЭОС-0,09/2-И1.
2.3.11. Сварочные материалы (электроды, флюсы, порошковую проволоку, проволоку сплошного сечения) следует выдавать сварщику в количестве, необходимом для односменной работы. Неиспользованные за смену электроды с покрытием основного вида и порошковую проволоку следует хранить в сушильных шкафах, а флюс - в закрытой таре.
При хранении прокаленных электродов с покрытием основного вида и порошковой проволоки в сушильных шкафах (с температурой 135-150°С), а флюсов - в закрытой таре срок их хранения не ограничивается.
2.3.12. Флюс, оставшийся после сварки, должен быть возвращен на участок подготовки, где его очищают от шлаковых включений, металлических примесей и других загрязнений.
2.3.13. Сварочную проволоку сплошного сечения перед выдачей на трубосварочную базу необходимо очистить от ржавчины, загрязнений и масел.
Порошковая проволока со следами ржавчины не подлежит сварке.
2.3.14. Назначение и области применения должны соответствовать данным, приведенным в табл.10-12:
электродов с покрытием основного вида (табл.10);
электродов с покрытием целлюлозного вида (табл.11);
сварочных материалов для автоматической сварки под флюсом поворотных стыков труб - флюсов и проволок (табл.12);
сварочных материалов для автоматической и полуавтоматической сварки неповоротных стыков труб в защитных газах (табл.13).
Таблица 10
Электроды с покрытием основного вида для сварки и ремонта поворотных и неповоротных стыков труб при любых условиях прокладки трубопроводов
Электроды | Свариваемые трубы |
Назначение | Тип по ГОСТ 9467-75 | Марка | Диаметр, мм | Толщина стенки, мм | Нормативное значение временного сопротивления разрыву, МПа (кгс/мм ) |
1 | 2 | 3 | 4 | 5 | 6 |
Для сварки, ремонта корневого слоя шва и подварки изнутри трубы | Э42А | УОНИ-13/45 | 2,0-2,5, 3,0 | 5-8 6-26 и более | До 490 (50) включительно |
| Э50А | УОНИ-13/55 | 2,0-2,6 | 5-8 | До 588 (60) включительно |
| | ЛБ-52У* НИБАЗ 55 Супербаз Фокс ЕВ 50 ОК 48.04 ВСО-50СК* | 2,5-3,25 | 8-26 и более | - |
Для сварки и ремонта заполняющих и облицовочных слоев шва (после "горячего" прохода электродами с целлюлозным покрытием или после сварки корневого слоя электродами с основным покрытием) | Э42А | УОНИ-13/45 | 3,0-4,0 | 5-26 и более | До 431 (44) включительно |
| Э50А | УОНИ-13/55 Гарант | 3,0-3,25 | 5-8 | До 539 (55) |
| | Фокс ЕВ 50 ОК 48.04 ОЗС-ВНИИСТ-27** | 4,0-5,0 | 6-26 и более | - |
| Э60 | ВСФ-65У ОЗС-24** Шварц-3К ОК 7379 | 3,0-3,25 | 5-8 | 539-588 (55-60) включительно |
| | ЛБ-62Д Нибаз 65 Кессель 5520 Мо | 4,0-5,0 | 6-26 и более | 538-588 (55-60) включительно |
| Э70 | ВСФ-75*** ЛБ-65Д ОК 74.78 | 4,0-5,0 | 10-26 и более | 588-637 (60-65) |
Примечание. Каждый диаметр (группа диаметров) электродов относится ко всем маркам электродов, сгруппированных согласно типу по ГОСТ 9467-75. Например, группа диаметров 2,0-2,6 относится ко всем маркам электродов типа Э50А от УОНИ-13/55 до ОК 48.04, то же самое для диаметра 3,0 и 3,25.
* Электроды ЛБ-52У и ВСО-50СК диаметром 3,0 мм - только для сварки корневого слоя шва.
** Электроды ОЗС-ВНИИСТ-27 и ОЗС-24 особо рекомендуются для наземной и надземной прокладок в районах Крайнего Севера.
*** Электроды ВСФ-75 предназначены для сварки стыков труб из термически упрочненных труб с нормативным пределом прочности 637 МПа (65 кгс/мм ). Электроды УОНИ-13/45 предпочтительнее применять для сварки труб из низкоуглеродистых нелегированных сталей типа Ст.20сп и т.п.; при сварке тонкостенных труб (толщина стенки 5-8 мм) для корневого слоя шва предпочтительнее электроды диаметром 2,0-2,6 мм.
Таблица 11
Электроды с покрытием целлюлозного вида для сварки неповоротных стыков труб при подземной прокладке трубопроводов
Электроды | Свариваемые трубы |
Назначение | Тип по ГОСТ 9467-7 | Марка | Диаметр, мм | Толщина стенки, мм | Нормативное значение временного сопротивления разрыву, МПа (кгс/мм ) |
1 | 2 | 3 | 4 | 5 | 6 |
Для сварки первого (корневого) слоя шва | Э42 | ВСЦ-4 Фокс Цель | 3,0-3,25 | 5-8 | До 568 (60) |
| | Кобе-6010 Пайпвелд-6010 Тиссен Цель 70 | 4,0 | | 6-26 |
| Э50 | ВСЦ-4А Кобе-7010 | 3,0-3,25 | 5-8 | 539-637 (55-65) включительно |
| | Пайпвелд-7010 | 4,0 | 6-26 и более | |
Для сварки второго слоя шва (горячего прохода) | Э42 | ВСЦ-4 Фокс Цель | 3,0-3,25 | 5-8 | До 588 (60) |
| | Кобе-6010 Пайпвелд-6010 Тиссен Цель 70 | 4,0 | 10-26 и более | |
| Э50 и Э60 | ВСЦ-4А, ВСЦ-60 Фокс Цель Мо Кобе-8010 Пайпвелд-7010 | 4,0-5,0 | 6-26 и более | 539-588 (55-60) включительно |
Для сварки заполняющих слоев шва | Э60 | ВСЦ-60 | 5,0 | 10-26 и более | 539-588 (55-60) включительно |
Таблица 12
Сварочные материалы для автоматической сварки под флюсом поворотных стыков труб
Способы сварки | Сочетание сварочных материалов | Характеристика свариваемых труб | Вид прокладки |
| Марка | Нормативное значение временного сопротивления разрыву, МПа (кгс/мм ) | |
| флюса | проволоки | | |
1 | 2 | 3 | 4 | 5 |
Односторонняя сварка по сваренному вручную корневому слою | АН-348А АНЦ-1 | СВ-08 СВ-08А СВ-08АА | До 490 (50) включительно | Подземная |
| АН-348АМ | (СВ-08ГА) | | |
| АН-47 | СВ-08 СВ-08А СВ-08АА (СВ-08ГА) | До 490 (50) включительно | Любая |
| АН-348А АН-348АМ | СВ-08ГА | Свьше 490 (50) до 539 (55) | Подземная |
| АН-47 | СВ-08ГА | Свыше 490 (50) до 539 (55) | Любая |
| АН-47 АН-ВС | СВ-08ХМ СВ-08МХ S 2Мо | 539-588 (55-60) включительно, в том числе термоупрочненных | " |
| ФЦ-16 | СВ-08ГНМ | 539-588 (55-60) включительно | " |
| АН-ВС | СВ-08ХГ2СНМТ | 637 (65) включительно | " |
Двусторонняя сварка | АН-348А АНЦ-1 АН-348АМ АН-47 | СВ-08ГА | До 588 (60) включительно | Подземная |
| АН-47 | СВ-08ГА | До 539 (55) | Любая |
| АН-47 АН-ВС | СВ-08МХ СВ-08ХМ S 2Мо СВ-08хГ2СМНТ | 539-588 (55-60) включительно, а также термически упрочненных с = 637 (65) | " |
| ФЦ-16 | СВ-08ГНМ | 539-588 (55-60) включительно | " |
Примечания:
1. При автоматической сварке труб с нормативным временным сопротивлением разрыву до 489 МПа предпочтительнее применение проволок СВ-08, СВ-08А, СВ-08АА.
2. При подварке корня шва автоматической сваркой под флюсом, а также при сварке током прямой полярности следует использовать те же самые материалы, которые рекомендованы для сварки заполняющих слоев.
3. При автоматической сварке (односторонней и двусторонней) термически упрочненных труб с нормативным пределом прочности 637 МПа из стали 17Г1С поставки Волжского трубного завода диаметром 1420 мм и нормативной толщиной стенки 15,1 мм следует применять флюс АН-ВС в сочетании со сварочной проволокой СВ-08ХГ2СНМТ.
Таблица 13
Способы сварки | Сочетание сварочных материалов | Характеристика свариваемых труб | Слои шва |
| Защитный газ | Сварочная проволока | Нормативное значение временного сопротивления разрыву, МПа (кгс/мм ) | |
1 | 2 | 3 | 4 | 5 |
Автоматическая сварка в защитных газах неповоротных стыков труб | Газовая смесь 25-75% аргона + 25-75% углекислого газа | Св-08ГС или Св-08Г2С | Менее 539 (55) | Внутренний корневой шов, наружный корневой шов |
| Углекислый газ | Св-08Г2С | То же | Заполняющие слои |
| Газовая смесь 25-75% аргона + 25-75% углекислого газа | Св-08Г2С | До 539-588 (55-60) включительно | Внутренний корневой шов, наружный корневой шов |
| Углекислый газ | Св-08Г2С | То же | Заполняющие слои |
| Газовая смесь 25-75% аргона + 25-75% углекислого газа | Св-08Г2С | До 637 (65) включительно | Внутренний корневой шов, наружный корневой шов |
| Углекислый газ | Св-08Г2СМ | То же | Заполняющие слои |
Полуавтоматическая сварка в защитных газах неповоротных стыков труб | Углекислый газ | Св-08ГС Св-08Г2С | До 539 (55) включительно | Все слои |
| | Св-08Г2С Св-08Г2СМ | Свыше 539 до 588 (55-60) | Корневой и заполняющие швы, заполняющие швы |
Сварочные материалы для сварки стыков труб с различным нормативным значением временного сопротивления разрыву устанавливают в соответствии с табл.10-13:
при различных значениях толщин стенок стыкуемых труб по более прочной трубе;
при одинаковых значениях толщин стенок стыкуемых труб по менее прочной трубе.
Порядок выдачи рекомендаций на применение новых сварочных материалов дан в обязательном приложении 4.
Примечание. Марки самозащитных порошковых проволок для механизированной сварки заполняющих слоев трубопроводов с принудительным формированием шва выбираются в зависимости от прочностного класса сталей: марку ПП-АН24СМ следует применять для сварки стыков труб из сталей с нормативным пределом прочности до 549 МПа, марки ПП-АН24СМ и ПП-АН19 - из сталей с нормативным пределом прочности до 589 МПа, марку ПП-АН30С - из сталей с нормативным пределом прочности 637 МПа.
2.4. Ручная электродуговая сварка кольцевых стыков труб
2.4.1. Ручную дуговую сварку следует выполнять с применением электродов, указанных в табл. 10-11. Запрещается вести сварку с применением любых присадок, подаваемых в дугу дополнительно или закладываемых в разделку.
2.4.2. Сварку первого (корневого) слоя шва электродами с целлюлозным покрытием ведут постоянным током обратной или прямой полярности, сварку "горячего" прохода и последующих слоев шва - электродами с целлюлозным покрытием на обратной полярности, а также сварку всех слоев шва электродами с основным покрытием - на постоянном токе обратной полярности.
Рекомендуемые значения сварочного тока приведены в табл.14 и табл.15.
Таблица 14
Рекомендуемые значения сварочного тока при сварке электродами с основным видом покрытия способом "на подъем"
Диаметр электродов, мм | Сварочный ток (А) в зависимости от пространственного положения шва |
| нижнее | вертикальное | потолочное |
2,0-2,5 | 50-90 | 40-80 | 40-50 |
3,0-3,25 | 90-130 | 80-120 | 90-110 |
4,0 | 140-180 | 110-170 | 150-180 |
Таблица 15
Рекомендуемые значения сварочного тока при сварке электродами способом "на спуск"
Диаметр электродов, мм | Слой | Сварочный ток (А) в зависимости от пространственного положения шва |
| | нижнее | вертикальное | потолочное |
Электроды с целлюлозным видом покрытия |
3,0-3,25 | 1 | 90-110 | 90-110 | 80-100 |
4,0 | 1 | 120-160 | 120-160 | 100-140 |
4,0 | "Горячий" проход | 140-180 | 150-170 | 140-170 |
5,0 | "Горячий" проход и заполняющие слои | 180-200 | 200-220 | 160-180 |
Электроды с основным видом покрытия |
3,0 | 1 | 80-100 | 110-130 | 90-110 |
2.4.3. При применении электродов с целлюлозным покрытием сварку следует осуществлять методом замочной скважины ("окна"). Когда в процессе сварки электросварщик поддерживает угол наклона электрода в пределах 40-90°, он должен вести "окно" за торцом электрода.
2.4.4. При вынужденных перерывах во время сварки первого (корневого) слоя шва необходимо поддерживать температуру торцов труб на уровне требуемой температуры предварительного подогрева. Если это условие было не соблюдено, то стык должен быть вырезан и заварен вновь.
2.4.5. После сварки корневого слоя шва электродами с целлюлозным видом покрытия обязательна его шлифовка абразивным инструментом.
2.4.6. "Горячий" проход является обязательной операцией, которую осуществляют непосредственно после сварки и шлифовки корневого слоя шва, выполненного с применением целлюлозных электродов.
"Горячим" проходом считается только такой проход, который выполнен по неостывшему корневому слою шва электродами с целлюлозным видом покрытия или специальными низководородистыми электродами, обеспечивающими возможность сварки "на спуск".
2.4.7. Время между окончаниями сварки первого слоя шва и началом выполнения "горячего" прохода не должно быть более 5 мин. Скорость сварки "горячего" прохода целлюлозными электродами - 18-20 м/ч.
2.4.8. При сварке заполняющих и облицовочного слоев шва труб с пределом прочности 539 МПа (55 кгс/мм ) и выше необходимо следить за тем, чтобы температура перед наложением каждого последующего слоя была не ниже +5°С. Если температура участка шва, подлежащего сварке, упала ниже +5°С, необходимо провести повторный подогрев.
2.4.9. При сварке корневого слоя шва электродами с основным видом покрытия "на спуск" дугу возбуждают методом "зажигания спички" на поверхности разделки, затем, чуть оторвав электрод от поверхности зажигания (длина дуги не более 1,5 мм), мгновенно переводят дугу на свариваемые кромки. Кратер необходимо выводить на поверхность разделки кромок или прорезать шлифмашинкой. После достижения контакта между втулочкой электрода и поверхностью разделки электрод перемещают сверху вниз без поперечных колебаний, непрерывно регулируя положение дуги относительно сварочной ванны. Промежуток "застывший сварочный шлак - дуга" регулируется изменением наклона электрода, скоростью его перемещения, усилием прижатия электрода к свариваемым кромкам и силой тока.
Примечание. Достижение сквозного проплавления фиксируется по характерному шуму проходящей "навылет" дуги.
2.4.10. Перемещать внутренний центратор разрешается только после того, как корневой слой шва полностью сварен электродами с целлюлозным покрытием или на 3/4 периметра стыка - электродами с основным покрытием. При сварке термоупрочненных труб при любых электродах корневой слой должен быть сварен полностью.
2.4.11. Сварной шов облицовочного слоя должен перекрывать основной металл в каждую сторону от шва на 2,5-3,5 мм и иметь усиление высотой 1-3 мм.
2.4.12. Стыки труб диаметром 1020 мм и более из сталей с нормативным пределом прочности 539 МПа (55 кгс/мм ) и выше должны быть подварены изнутри электродами с основным видом покрытия.
2.4.13. Для диаметров, указанных в п.2.4.12, подварку поворотных стыков, а также стыков разностенных труб, деталей трубопроводов, запорной и распределительной арматуры выполняют по всему периметру.
2.4.14. Для диаметров, указанных в п.2.4.12, подварку неповоротных стыков в случае сварки корневого слоя электродами с основным покрытием способом "на подьем" осуществляют на нижней четверти периметра и на участках стыка с непроваром. Подварку неповоротных стыков при сварке корневого слоя электродами с целлюлозным покрытием или основного вида типа ВСО-50СК, а также аналогичными им, необходимо производить на участках стыка с непроварами.
Подварку выполняют перед началом сварки заполняющих слоев шва. Запрещается производить подварку способом сварки "на спуск".
Подварочный слой должен иметь ширину 8-10 мм и усиление высотой 1-3 мм.
2.4.15. Чтобы предупредить образование дефектов между слоями перед наложением каждого последующего слоя шва, поверхность предыдущего шва должна быть очищена от шлака и брызг наплавленного металла. После окончания сварки поверхность облицовочного слоя шва также должна быть очищена от шлака и брызг.
2.4.16. Минимально допустимое число слоев шва при ручной дуговой сварке указано в табл.16.
Таблица 16
Толщина стенки трубы, мм | Минимальное число слоев шва при сварке корневого слоя шва электродами с разным видом покрытия |
| целлюлозный | основной |
До 10 | 3 | 2 |
Свыше 10-15 | 4 | 3 |
Свыше 15-20 | 5 | 4 |
Свыше 20-25 | 6 | 5 |
Свыше 25-32 | 7 | 6 |
2.4.17. Сварные соединения разрешается оставлять незаконченными только на одни сутки после окончания рабочего дня или при остановке работ, если число выполненных слоев шва соответствует табл.17. Если число слоев не соответствует данным, приведенным в табл.17, стык должен быть вырезан и заварен вновь.
Таблица 17
Толщина стенки трубы, мм | Необходимое число слоев при сварке корневого слоя шва электродами с разным видом покрытия |
| целлюлозный | основной |
До 10 | Стык заваривается полностью |
Свыше 10-15 | 3 | 2 |
Свыше 15 | 4 | 3 |
Примечание . Число слоев указано без учета подварочного слоя.
2.4.18. При ширине разделки более 30 мм рекомендуется применять многоваликовую сварку заполняющих и облицовочных слоев шва (рис.4).
Рис. 4. Схема выполнения заполняющих и облицовочного (а), только облицовочного (б) слоев шва несколькими валиками:
1-13 слои шва; В - ширина валика
2.4.19. Перед возобновлением сварки незавершенного стыка труб при температуре окружающего воздуха +5°С и ниже, а также при наличии влаги стык должен быть просушен.
2.5. Двусторонняя автоматическая сварка
под флюсом на базах типа БТС
2.5.1. Перед сваркой необходимо осуществить подготовительные операции и обработку кромок
2.5.2. В зависимости от типа применяемого оборудования последовательность наложения слоев шва может быть следующей:
сварка наружных слоев шва и последующая сварка внутреннего слоя;
сварка первого наружного слоя и последующая одновременная сварка второго наружного и внутреннего слоя шва.
2.5.3. Режимы сварки наружных и внутренних слоев шва малоуглеродистых и низколегированных горячекатаных и нормализованных сталей приведены в табл.18, термически упрочненных и из труб с контролируемой прокаткой - в табл.19.
Таблица 18
Диаметр трубы, мм | Толщина стенки, мм | Диаметр электродной проволоки, мм | Порядковый номер слоя | Ток, А | Напряжение, В | Скорость сварки, м/ч | Смещение электрода с зенита (надира), мм |
1 | 2 | 3 | 4 | 5 | 6 | 7 | 8 |
Наружная сварка | Против вращения трубы |
720-820 | 6,0-11,0 | 3 | 1 | 400-700 | 40-44 | 35-45 | 30-50 |
720-820 | 11,0-18,0 | 3 | 1 | 550-650 | 40-44 | 30-40 | 30-35 |
| | | Последующие | 600-700 | 44-46 | 35-40 | 20-40 |
720 | 18,1-22,0 | 3 | 1 | 700-750 | 42-44 | 40-45 | 30-50 |
| | | Последующие | 750-800 | 44-46 | 50-55 | 30-40 |
| | | Облицовочный | 700-750 | 46-48 | 40-50 | 20-40 |
| | 4 | 1 | 850-900 | 42-44 | 45-50 | 30-50 |
| | | Последующие | 900-950 | 44-46 | 50-55 | 30-40 |
| | | Облицовочный | 850-900 | 46-48 | 40-50 | 20-40 |
1020-1220 | 9,0-11,0 | 3 | 1 | 600-700 | 40-44 | 35-45 | 50-70 |
1020-1220 | 11,0-18,0 | 3 | 1 | 650-800 | 42-44 | 40-50 | 50-70 |
| | | Последующие | 700-800 | 44-46 | 35-45 | 40-60 |
1020-1220 | 18,1-27,0 | 3 | 1 | 800-900 | 42-44 | 40-50 | 60-80 |
| | | Последующие | 800-1000 | 44-46 | 45-55 | 40-60 |
| | | Облицовочный | 750-800 | 46-48 | 40-45 | 40-60 |
1020-1220 | 18,1-27,0 | 4 | 1 | 900-1000 | 42-44 | 40-50 | 60-80 |
| | | Последующие | 1000-1100 | 44-46 | 55-65 | 40-60 |
| | | Облицовочный | 850-900 | 46-48 | 40-50 | 40-60 |
1420 | 15,7-18,0 | 3 | 1 | 800-900 | 42-44 | 50-55 | 60-80 |
| | | Последующие | 750-800 | 44-46 | 40-50 | 60-80 |
1420 | 18,1-20,5 | 3 | 1 | 900-1000 | 42-44 | 45-55 | 60-80 |
| | | Последующие | 850-900 | 44-46 | 45-55 | 60-80 |
| | | Облицовочный | 800-850 | 46-48 | 40-50 | 40-60 |
| | 4 | 1 | 950-1050 | 44-46 | 50-60 | 60-80 |
| | | Последующие | 1000-1100 | 44-46 | 60-70 | 60-80 |
| | | Облицовочный | 850-900 | 46-48 | 40-50 | 40-60 |
1420 | 20,6-32,0 | 4 | 1 | 950-1100 | 44-46 | 50-60 | 60-80 |
| | | Последующие | 1100-1200 | 44-46 | 60-70 | 60-80 |
| | | Облицовочный | 850-900 | 46-48 | 40-50 | 40-60 |
720-1220 | 6,0-11,0 | 3 | 1 | 400-600 | 42-46 | 35-45 | 15-20* |
720-1420 | 11,1-18,0 | 3 | 1 | 600-800 | 42-46 | 35-45 | 15-20 |
720-1420 | 18,1-32,0 | 3 | 1 | 700-850 | 42-46 | 40-50 | 15-20 |
720-1420 | 18,1-32,0 | 4 | 1 | 700-900 | 42-46 | 40-50 | 15-25 |
Примечание. Вылет электрода - 40-45 мм; полярность обратная; при сварке под флюсом АН-ВС толщин до 20,5 мм величину сварочного тока рекомендуется увеличить на 100-200 А при скорости сварки 60-100 м/ч; угол наклона электрода "вперед" - до 30°.
Таблица 19
Смещение электрода с надира трубы.
Диаметр трубы, мм | Толщина стенки, мм | Порядковый номер слоя | Сварочный ток, А | Напряжение, В | Скорость сварки, м/ч | Смещение электрода с зенита, мм |
Наружная сварка |
820-1420 | 8,0-15,1 | 1 | 500-700 | 40-44 | 40-45 | 40-80 |
| | Последующий | 650-700 | 44-46 | 40-55 | 40-60 |
1420 | 15,7-20,5 | 1 | 700-750 | 42-44 | 45-55 | 60-80 |
| | Последующий | 600-650 | 44-46 | 40-50 | 40-60 |
| 20,6-32,0 | 1 | 700-750 | 40-44 | 40-50 | 60-80 |
| | Последующий | 750-800 | 44-46 | 55-60 | 40-60 |
| | Облицовочный | 700-750 | 46-48 | 40-50 | 40-60 |
Внутренняя сварка |
820-1420 | 8,0-32,0 | 1 | 500-800 | 40-44 | 40-50 | По вращению или против вращения трубы 15-20* |
Примечание. Полярность обратная. Вылет электрода 40-45 мм. Сварку выполнять только проволокой диаметром 3 мм. Угол наклона электрода "вперед" до 30°.
Смещение электрода с надира трубы.
2.5.4. Число наружных слоев и ширина шва на последнем слое в зависимости от диаметра и толщины стенки труб приведены в табл.20. Внутренний шов сваривают в один слой. Величина усиления внутреннего и наружного шва должна находиться в пределах 1-3 мм.
Таблица 20
Диаметр трубы, мм | Толщина стенки трубы, мм | Минимальное число наружных слоев | Ширина облицовочного наружного шва, мм |
720 | От 6,0 до 11,5 | 1 | 18 ±3 |
| Свыше 11,5 до 15,0 | 2 | 20 ±3 |
| " 15,0 до 17,5 | 3 | 20 ±3 |
| " 17,5 до 22,0 | 3 | 22 ±4 |
820 | От 8,0 до 11,5 | 1 | 18 ±3 |
| Свыше 11,5 до 15,0 | 2 | 20 ±3 |
1020-1220 | От 10,5 до 11,5 | 1 | 18 ±3 |
| Свыше 11,5 до 17,5 | 2 | 18 ±3 |
| " 17,5 до 21,5 | 2 | 22 ±4 |
| " 21,5 до 24,0 | 3 | 22 ±4 |
| " 24,1 до 27,0 | 4 | 24 ±4 |
1420 | От 15,8 до 20,5 | 2 | 22 ±4 |
| Свыше 20,5 до 24,0 | 3 | 24 ±4 |
| " 24,0 до 28,0 | 4 | 30 ±4 |
| " 28,0 до 32,0 | 5 | 32 ±4 |
2.5.5. Геометрические размеры швов определяют на макрошлифах, изготовленных из каждого 200 стыка. Геометрические размеры швов, определяемые по макрошлифам, должны соответствовать данным рис.6 и табл.21. В случае отклонения геометрических параметров швов от заданных (см. рис.6, табл.21) сварку следует прекратить, отладить оборудование и режим сварки
1 - ось первого (наружного) слоя шва;
2 - ось внутреннего слоя шва;
3 - условная ось стыка; - перекрытие наружного и внутреннего слоев шва ( 3 мм при толщине стенки трубы 12 мм и более, 2 мм при толщине стенки менее 12 мм); - смещение осей наружных и внутреннего слоев шва от условной оси стыка ( = ±1 мм); и - глубина проплавления соответственно первого (наружного) и внутреннего слоев шва; - ширина внутреннего шва (табл.21)
Таблица 21
Толщина стенки, мм | Тип разделки кромок (см. рис.5) | Размеры внутреннего шва* (не более), мм |
| | глубина проплавления | ширина шва |
6,0 | а | 4 | 15 |
9,5-11,0 | а | 6 | 15 |
11,1-15,2 | б | 7 | 21 |
15,3-18,0 | б | 9 | 26 |
18,1-21,0 | в | 10 | 26 |
19,7-20,5 | г | 12 | 26 |
21,1-32,0 | г | 12 | 28 |
Остальные 199 стыков, предшествующие вырезанному, следует считать годными, если в результате контроля просвечиванием в них не обнаружено недопустимых дефектов.
Если наружный облицовочный слой шва смещен относительно первого наружного слоя, стык считается годным при отсутствии в нем недопустимых дефектов и соблюдении заданных режимов. При этом оси наружного корневого и внутреннего швов должны совпадать или быть смещены относительно друг друга на величину не более 2 мм (рис.7).
Рис.7. Внешний вид макрошлифов сварных швов при двусторонней автоматической сварке под флюсом и симметричном и несимметричном расположении первого (наружного) и внутреннего слоев шва:
1 - первый (наружный) слой шва;
2 - облицовочный слой шва;
3 - внутренний слой шва
2.5.6. Для предотвращения непроваров и шлаковых включений автоматическую сварку прихваток и начального участка шва не следует выполнять при значениях тока ниже нижнего предела диапазона режимов сварки.
2.5.7. При заклинивании шлака в разделке во время сварки первого наружного слоя и для получения благоприятной менискообразной формы шва смещение электрода с зенита трубы должно быть на 5,0-10,0 мм выше значений, указанных в табл.18 и 19.
2.5.8. Начало и окончание сварки стыка должно располагаться на расстоянии не менее 100 мм от продольных швов свариваемых труб.
2.5.9. Во избежание образования шлаковых включений и непровара между первым наружным и внутренним слоями в начале прихватки или первого слоя шва рекомендуется делать шлифмашинкой пропил глубиной 4-5 мм, шириной 3-4 мм и длиной не менее 25-30 мм.
2.5.10. Чтобы избежать образования трещин, запрещается освобождать жимки центратора до полного завершения процесса сварки первого наружного слоя стыка.
2.5.11. Интервал времени между завершением первого наружного слоя шва и началом сварки внутреннего слоя не должен превышать:
1 ч при положительной температуре воздуха;
30 мин при температуре воздуха ниже нуля.
Интервал времени между сваркой предыдущего и каждого из последующих наружных слоев шва не должен превышать 2 ч.
2.5.12. Если сварку выполняют при отрицательных температурах, то запрещается скатывать сваренную плеть на мокрый грунт или снег до тех пор, пока стык не остынет до температуры окружающей среды.
2.5.13. В конце смены стыки труб должны быть заварены полностью. В порядке исключения, в случае выхода из строя оборудования, отключения сети и т.д. стыки труб до следующей смены разрешается оставлять с несваренным облицовочным слоем шва. При невыполнении указанного требования стыки подлежат вырезке.
2.6. Односторонняя автоматическая сварка под флюсом на базах типа ССТ-ПАУ
2.6.1. Ручная подварка корня шва осуществляется в соответствии с подразд.2.4 настоящих ВСН.
2.6.2. Для улучшения отделимости шлаковой корки после выполнения корневого слоя шва допускается ручная дуговая сварка дополнительных слоев. Дополнительный (е) слой шва сваривают только после полного завершения корневого слоя шва по всему периметру стыка.
2.6.3. Нельзя начинать прихватку или ручную дуговую сварку корневого слоя шва на расстоянии менее 100 мм от продольного шва трубы.
2.6.4. Автоматическую подварку корня шва под флюсом выполняют по всему периметру стыка теми же материалами, которые рекомендованы для сварки заполняющих слоев, после сварки корневого слоя шва или после выполнения всех наружных слоев.
2.6.5. Если подварку осуществляют после сварки корневого слоя шва, то интервал между окончанием сварки корня шва и началом сварки подварочного слоя не должен превышать 40 мин.
2.6.6. Если подварку выполняют после завершения сварки наружных слоев шва, то интервал времени между окончанием сварки корня шва и началом выполнения подварочного слоя не должен превышать 1,5 ч.
2.6.7. Подварку стыков труб диаметрами 1020-1420 мм следует выполнять в один слой на режимах, приведенных в табл.22.
Таблица 22
Вид труб | Схема выполнения подварки | Диаметр электродной проволоки, мм | Сварочный ток, А | Напря- жение на дуге, В | Скорость сварки, м/ч | Вылет элект- рода, мм. | Смещение с надира в направлении вращения трубы, мм |
1 | 2 | 3 | 4 | 5 | 6 | 7 | 8 |
Трубы из горячекатаных, нормализованных сталей и сталей контролируемой прокатки (до 588 мПа) | После сварки корня шва | 3 | 450-300 | 44-46 | 25-30 | 30-35 | 30-35 |
| | 4 | 550-600 | 44-46 | 30-40 | 40-50 | 30-50 |
| После завершения всех наружных слоев шва | 3 | 550-600 | 44-46 | 30-35 | 30-35 | 30-50 |
| | 4 | 600-650 | 44-46 | 30-40 | 40-50 | 30-50 |
Трубы из термически упрочненных сталей 588-637 МПа | После сварки корня шва | 3 | 350-450 | 44-46 | 30-40 | 30-35 | 30-50 |
| После завершения всех наружных слоев шва | 3 | 550-650 | 42-46 | 40-50 | 30-35 | 30-50 |
Примечания:
1. Режимы приведены для сварки на постоянном токе обратной полярности при угле наклона электрода, равном нулю.
2. Подварку корня шва термически упрочненных сталей следует выполнять электродной проволокой диаметром 3 мм при значениях погонной энергии не более 23 кДж/см.
2.6.8. Шов, полученный при автоматической подварке, должен иметь усиление не менее 1 и не более 3 мм, а ширину в пределах, указанных в табл.21 для внутреннего слоя шва.
2.6.9. Глубина проплавления при автоматической подварке не должна превышать значений, регламентированных табл.21.
2.6.10. Смещение осей наружных и внутренних слоев шва от условной оси стыка не должно превышать ±1,0 мм.
2.6.11. Контроль параметров по пп.2.6.9, 2.6.10 осуществляют на макрошлифах в соответствии с п.2.6.8 и с рис.6.
2.6.12. Автоматическую сварку заполняющих слоев шва под флюсом применяют для соединения труб диаметром 325-1420 мм с толщиной стенки до 32 мм включительно. Режимы автоматической сварки заполняющих слоев шва труб из горячекатаных, в том числе с контролируемой прокаткой, нормализованных и термически упрочненных сталей приведены в табл.23.
Таблица 23
Диаметр труб, мм | Толщина стенки, мм | Диаметр электродной проволоки, мм | Слои шва | Сварочный ток, А | Напряжение, В | Скорость сварки, м/ч | Смещение электрода с зенита, мм |
1 | 2 | 3 | 4 | 5 | 6 | 7 | 8 |
325-426 | 6 | 2 | 1 | 350-450 | 34-36 | 15-20 | 35-40 |
| | | Последующие | 350-450 | 36-38 | 15-20 | 30-35 |
| 7-12,5 | 2 | 1 | 400-500 | 34-36 | 30-35 | 35-40 |
| | | Последующие | 450-500 | 36-38 | 30-35 | 30-40 |
| Более 12,5 | 3 | 1 | 500-600 | 34-36 | 25-35 | 35-40 |
| | | Последующие | 650-750 | 36-38 | 30-40 | 30-40 |
530-820 | 6-12,5 | 2 | 1 | 400-500 | 42-44 | 35-40 | 60-80 |
| | | Последующие | 500-550 | 42-46 | 35-40 | 40-50 |
| | 3 | 1 | 550-650 | 42-44 | 35-50 | 40-60 |
| | | Последующие | 700-750 | 44-46 | 35-50 | 30-40 |
530-820 | Более 12,5 | 3 | 1 | 550-650 | 42-44 | 35-50 | 40-60 |
| | | Последующие | 680-750 | 44-46 | 35-50 | 30-40 |
1020-1220 | 7-12,5 | 3 | 1 | 550-650 | 44-46 | 40-50 | 60-80 |
| | | Последующие | 650-750 | 46-48 | 40-50 | 40-60 |
| | 4 | 1 | 800-900 | 44-46 | 45-50 | 60-80 |
| | | Последующие | 900-950 | 46-48 | 45-55 | 40-60 |
1020-1220 | Более 12,5 | 3 | 1 | 750-800 | 44-46 | 45-55 | 60-80 |
| | | Последующие | 800-850 | 46-48 | 40-55 | 40-60 |
| | 4 | 1 | 800-900 | 44-46 | 45-55 | 60-80 |
| | 4 | Последующие | 1000-1100 | 46-48 | 70-90 | 40-60 |
| | 4 | Облицовочный | 800-900 | 46-48 | 40-50 | 40-60 |
1420 | 9-16 | 3 | 1 | 750-800 | 44-46 | 40-50 | 80-100 |
| | | Последующие | 800-850 | 46-48 | 40-50 | 40-80 |
| | 4 | 1 | 800-900 | 44-46 | 40-55 | 80-100 |
| | | Последующие | 800-900 | 46-48 | 40-50 | 40-80 |
1420 | Более 16 | 3 | 1 | 750-800 | 44-46 | 40-50 | 60-100 |
| | | Последующие | 800-850 | 44-46 | 50-55 | 60-80 |
| | | Облицовочный | 850-900 | 46-48 | 40-50 | 40-80 |
| | 4 | 1 | 800-900 | 44-46 | 40-55 | 80-100 |
| | | Последующие | 1000-1100 | 44-46 | 70-90 | 60-80 |
| | | Облицовочный | 800-900 | 46-48 | 40-50 | 40-80 |
Примечания:
1. Режимы даны для сварки постоянным током обратной полярности.
2. При сварке термически упрочненных труб запрещается применять сварочную проволоку диаметром 4 мм.
3. При сварке труб большого диаметре под флюсом АН-ВС величину тока рекомендуется увеличить на 100-200 А.
4. При сварке заполняющих и облицовочного слоев шва под флюсом АН-ВС скорость сварки увеличивается до 100 м/ч.
5. Вылет электрода диаметром 2 мм - 30-35мм, 3 мм - 40-45 мм, 4 мм - 40-50 мм; угол наклона электрода "вперед" - до 30°.
2.6.13. Допускается автоматическая сварка под флюсом труб диаметром 219-273 мм, режимы сварки которых приведены в табл.24.
Таблица 24
Диа- метр трубы, мм | Тол- щина стенки трубы, мм | Диаметр элект- родной про- волоки, мм | Слои шва | Сварочный ток, А | Напря- жение на дуге, В | Ско- рость сварки, м/ч | Вылет элект- родной про- волоки, мм | Сме- щение элект- родной про- волоки с зенита, мм | Угол наклона элект- родной проволоки по направ- лению сварки, град |
219 | 6 | 2 | Первый | 300-560 | 34-36 | 14 | 35-40 | 60 | До 12 |
| | | Последующие | 320-340 | 36-38 | 14 | 35-40 | 60 | До 12 |
275 | 6 | 2 | Первый | 360-440 | 34-36 | 14 | 35-40 | 60 | До 15 |
| | | Последующие | 360-440 | 36-38 | 14 | 35-40 | 60 | До 15 |
2.6.14. Автоматическую сварку труб с повышенной толщиной стенки (более 23 мм) целесообразно проводить электродной проволокой диаметром 3-4 мм с применением флюса ФЦ-16, обеспечивающего удаление шлаковой корки из узкой разделки после выполнения первого прохода шва.
В этом случае сварку первого слоя шва рекомендуется осуществлять по центру узкой разделки током 500-600 А при напряжении на дуге 30-32 В и скорости сварки 25-40 м/ч.
2.6.15. При сварке толстостенных труб разрешается наложение заполняющих (первого, второго и т.д.) и облицовочного слоев шва параллельными (с перекрытием) проходами (рис.8). В этом случае напряжение горения дуги снижают на 2-4 В и скорость сварки увеличивают не менее чем на 20%.
Рис.8. Рекомендуемая схема наложения швов при односторонней автоматической сварке под флюсом кольцевых стыков труб параллельными проходами:
1-8 - порядковые номера слоев
2.6.16. Число слоев (без учета подварочного слоя), выполненных автоматической сваркой под флюсом, зависит от толщины стенки труб:
Толщина стенки трубы, мм | Число слоев шва (не менее) |
До 16,5 | 2 |
Свыше 16,5 до 20,5 | 3 |
" 20,5 до 24,0 | 4 |
" 24,0 до 28,0 | 5 |
" 28,0 до 32,0 | 6 |
2.6.17. Ширина облицовочного шва, выполненного двумя параллельными с перекрытием слоями (проходами), не должна превышать допустимой ширины однопроходного облицовочного шва в соответствии с табл.25. Сопряжение облицовочных швов между собой и основным металлом должно быть плавным.
Таблица 25
Толщина стенки трубы, мм | Ширина сварного шва, мм |
От 6 до 8 | 14 ±4 |
Свыше 8 до 12 | 20 ±4 |
" 12 до 16 | 24 ±4 |
" 16 до 20,5 | 26 ±4 |
" 20,5 до 28 | 32 ±4 |
" 28 до 32 | 34 ±4 |
2.6.18. Если значения сварочного тока превышают 600 А, то автоматическую сварку под флюсом целесообразно выполнять током прямой полярности. При этом ток следует увеличить на 100 А, а скорость сварки установить по верхнему пределу диапазона скоростей, указанного в табл.23. Все остальные параметры режима сварки, указанные в табл.23, оставить без изменения.
2.6.19. При переходе на прямую полярность после отработки режимов сварки необходимо сварить допускной стык и испытывать его в соответствии со СНиП III-42-80.
2.6.20. Автоматическую сварку током прямой полярности следует выполнять теми же сварочными материалами, которые применяют при сварке на обратной полярности.
2.6.21. Интервал времени между сваркой предыдущего автоматического наружного слоя и каждого из последующих слоев шва не должен превышать 2 ч. Сварные соединения разрешается оставлять в конце смены незаконченными в том случае, если не сварен только облицовочный слой шва. Указанные стыки должны быть обязательно подварены изнутри трубы. При невыполнении указанных требований стыки подлежат вырезке.
Сварные соединения на базах типа БНС (база наружной сварки) оставлять незаконченными не разрешается.
2.6.22. Для предотвращения увлажнения стыков в случае непогоды (дождь, снег, иней) стыки, сваренные корневым слоем шва, перед автоматической сваркой под флюсом должны быть укрыты влагоустойчивыми поясами шириной не менее 250-300 мм. Если стыки, сваренные корневым слоем шва, попадают на пост автоматической сварки со следами влаги (снега, инея и т.д.) на кромках, их необходимо просушить в соответствии с требованиями настоящих ВСН.
2.7. Автоматическая сварка неповоротных стыков трубопроводов порошковой проволокой с принудительным формированием
2.7.1. В процессе сварки следует выдерживать определенную глубину сварочной ванны внутри плавильного пространства. Расстояние от поверхности ванны до передней кромки ползуна должно составлять 7-10 мм для порошковой проволоки ПП-АН24СМ и ПП-АН30С и 3-7 мм - для порошковой проволоки ПП-АН19. Регулировка положения дуги по высоте плавильного пространства обеспечивается остановкой сварочной головки без прекращения подачи проволоки и горения дуги или увеличением скорости движения. В первом случае дуга и сварочная ванна поднимаются к переднему торцу ползуна, во втором - опускаются в глубь плавильного пространства.
2.7.2. Для качественного выполнения замка в зените трубы (в нижнем положении) сварку первой головкой завершают на скорости, превышающей скорость заполнения разделки в 1,5-2 раза, что позволяет получить плавный переход к последующему слою. Второй головкой наезжают на образовавшийся скос, формирующий ползун приостанавливают, не доходя 10-15 мм до начала предыдущего слоя и заплавляют промежуток между слоями. При подходе головки к зениту трубы целесообразно несколько увеличить амплитуду колебаний, а напряжение на дуге уменьшить на 1-2 В.
2.7.3. По окончании сварки стыка производится осмотр и ручная дуговая подварка неудовлетворительно сформированных участков.
2.7.4. Ремонт неудовлетворительно сформированных участков производят в соответствии с указаниями в подразделе 2.10 настоящих ВСН.
2.7.5. При сварке по ручной подварке к сборке под последующую автоматическую сварку порошковой проволокой допускают трубы с заводской разделкой кромок, а также с кромками, обрезанными механизированной или ручной газовой резкой. В этом случае прямолинейность реза должна обеспечивать прохождение формирующего ползуна с зазором между боковыми стенками его выступа и кромками в пределах не более 1-1,5 мм. Чешуйчатость поверхности реза после ручной газовой резки должна быть зачищена шлифмашинкой.
2.7.6. Кромки и прилегающие к ним внутренняя и наружная поверхности труб шириной не менее 10 мм перед сборкой должны быть зачищены до чистого металла. Попадание влаги, масла и грязи в разделку кромок следует исключить. Для прохода формирующего ползуна наружное усиление продольного (спирального) шва должно быть снято до 0-0,5 мм на расстоянии не менее 25 мм от кромки.
2.7.7. Для прохода сварочной головки высота лежек должна обеспечивать расстояние не менее 600 мм между трубой и грунтом, а расстояние от стыка до края опоры должно быть не менее 2 мм.
2.7.8. Толщина корневого слоя под автоматическую сварку приведена в табл.26 для проволоки диаметром 2,4 мм и в табл.27 - для проволок диаметром 2,0 и 2,6 мм (величина ее должна быть не менее 5 мм). Внутренняя подварка стыков диаметром 1020 мм и более должна осуществляться в соответствии с подразделом 2.4 настоящих ВСН.
2.7.9. При сварке труб диаметром 1020-1420 мм для уменьшения вероятности прожога в потолочном положении при толщине корневого слоя 5 мм внутренняя подварка обязательна на нижней четверти периметра стыка независимо от вида покрытия электродов, использованных при ручной сварке корня шва. При сварке труб диаметром 530-820 мм толщину корневого слоя шва во избежание прожога следует увеличивать снаружи.
2.7.10. Порошковую проволоку диаметром 2,0 мм следует использовать при сварке облицовочного слоя труб с толщиной стенки 9,5-10 мм. При использовании проволоки диаметром 2,4 мм для улучшения условий стабильности процесса сварки и формирования сварного соединения глубину формирующей канавки на водоохлаждаемом ползуне следует увеличить на 1 мм.
2.7.11. Поверхность корневого шва перед автоматической сваркой во избежание местных непроваров и шлаковых включений должна быть очищена от шлака, наплывов и крупной чешуи с применением шлифовальных кругов более тщательно, чем перед последующей ручной сваркой и иметь плавный переход к основному металлу.
2.7.12. Автоматическую сварку порошковой проволокой с принудительным формированием по ручной подварке осуществляют в один или несколько слоев в зависимости от толщины стенки трубы и диаметра проволоки. Число слоев и их толщина приведены в табл.26 (для проволоки диаметром 2,4 мм) и 27 (для проволоки диаметром 2,0 и 2,6 мм).
Таблица 26
Вид слоя | Высота слоя при толщине трубы, мм |
| До 10 | 10,1-12,0 | 13,1-14,0 | 14,1-17,0 | 17,1-20,0 | 20,1-23,0 | 22,1-26,0 |
Корневой слой (ручная сварка) | 5* | 6-7* | 6-7* | 8-9** | 6-7* | 6-7 | 6-7* |
1-й заполняющий слой (автоматическая сварка) | - | - | - | - | 6-7 | 7-8 | 6-7 |
2-й заполняющий слой (автоматическая сварка) | - | - | - | - | - | - | 6 |
Облицовочный слой (автоматическая сварка) | 5 | 5-6 | 7-8 | 8-9 | 6-7 | 8-9 | 6-7 |
Два прохода электродами с целлюлозным видом покрытия, либо один проход электродами с основным видом покрытия.
То же с дополнительным проходом, выполненным электродами с основным видом покрытия.
Таблица 27
Вид слоя | Высота слоя при толщине стенки трубы, мм |
| До 10 | 10,1-12,0 | 12,1-15,0 | 15,1-17,0 | 17,1-20,0 | 20,1-23,0 | 23,1-26,0 |
Корневой слой (ручная сварка) | 5 | 6-7 | 6-7 | 5 | 5 | 6-7 | 6-7 |
1-й заполняющий слой (автоматическая сварка) | - | - | - | 6* | 7-8 | 7-8** | 6** |
2-й заполняющий слой (автоматическая сварка) | - | - | - | - | - | - | 6** |
Облицовочный слой (автоматическая сварка) | 5 | 5-6 | 7-8 | 5-6* | 7-8* | 8-9** | 7-8** |
Сварка проволокой диаметром 2,0 мм.
Сварка проволокой диаметром 2,6 мм.
2.7.13. При сварке заполняющих слоев применяют формирующие ползуны с выступом, а при сварке облицовочных слоев - ползуны с канавкой по форме усиления. В зависимости от диаметра труб, толщины стенки и номера слоя высоту и ширину выступа необходимо подгонять таким образом, чтобы обеспечить высоту слоя в соответствии с табл.26 и 27, а зазор между боковыми стенками выступа ползуна и стенками разделки кромок должен быть не более 1-1,5 мм.
Канавка ползуна должна перекрывать разделку. Поверхность канавки и выступа ползуна после сварки каждых 3-5 стыков должны зашлифовываться от задиров для улучшения качества поверхности швов.
2.7.14. Сварку стыка осуществляют двумя сварочными головками, расположенными на противоположных сторонах трубы и работающими одновременно или поочередно.
2.7.15. Режимы сварки порошковой проволокой диаметром 2,4 мм приведены в табл.28, а порошковыми проволоками диаметром 2,0 и 2,6 мм - в табл.29. При этом следует иметь в виду, что уменьшение напряжения на дуге приводит к появлению несплавлений по кромкам, а увеличение напряжения - к появлению газовых пор. Сварку выполняют на постоянном токе обратной полярности от источников тока с жесткой (пологопадающей) вольтамперной характеристикой.
Таблица 28
Марка проволоки | Толщина стенки трубы, мм | Вид шва | Сварочный ток, А | Напряжение на дуге, В |
1 | 2 | 3 | 4 | 5 |
ПП-АН19 | До 17,0 мм включительно | Облицовочный | 300-350 | 26-28 |
| 17,1-23,0 | Заполняющий | 260-300 | 25-27 |
| | Облицовочный | 300-350 | 26-28 |
| 23,1-26,0 | 1-й заполняющий | 260-300 | 25-27 |
| | 2-й заполняющий | 280-320 | 25-27 |
| | Облицовочный | 300-350 | 27-29 |
ПП-АН24 ПП-АН24СМ | До 17,0 мм включительно | Облицовочный | 300-400 | 25-29 |
| 17,1-23,0 | Заполняющий | 280-320 | 24-28 |
| | Облицовочный | 300-400 | 26-31 |
| 23,1-26,0 | 1-й заполняющий | 280-320 | 24-28 |
| | 2-й заполняющий | 300-350 | 25-29 |
| | Облицовочный | 300-400 | 26-30 |
ПП-АН30 | До 17 мм включительно | Облицовочный | 300-360 | 26-29 |
| 17,1-23,0, | Заполняющий | 280-320 | 24-26 |
| | Облицовочный | 300-360 | 26-29 |
| 23,1-26,0 | 1-й заполняющий | 280-320 | 24-26 |
| | 2-й заполняющий | 280-340 | 26-29 |
| | Облицовочный | 300-360 | 26-30 |
Таблица 29
Диаметр проволоки, мм | Толщина стенки трубы, мм | Вид шва | Сварочный ток, А | Напряжение на дуге, В |
1 | 2 | 3 | 4 | 5 |
2,0 | 9,5-20,0 | Заполняющий | 250-280 | 22-25 |
| | Облицовочный | 280-320 | 24-28 |
2,6 | 20,1-26,0 | 1-й заполняющий | 250-400 | 25-30 |
| | 2-й заполняющий | 280-320 | 26-29 |
| | Облицовочный | 300-500 | 27-31 |
2.7.16. Величина вылета электродной проволоки зависит от ее диаметра и составляет для проволоки диаметром 2,0 мм 20-30 мм, для проволоки диаметром 2,4 мм 30-50 мм, для проволоки диаметром 2,6 мм 40-50 мм.
2.7.17. Сварку слоев шириной более 12-13 мм необходимо выполнять с поперечными колебаниями электрода, амплитуда которых устанавливается таким образом, чтобы в зоне сварки электродная проволока приближалась к свариваемым кромкам не менее чем на 2,5 мм. Частота колебаний составляет 0,5-2 Гц. Меньшая частота соответствует меньшей скорости сварки.
2.7.18. Замки предыдущего и последующего слоев должны быть смещены один относительно другого на расстояние не менее 60 мм.
2.7.19. Перед выполнением каждого последующего прохода поверхность предыдущего шва тщательно очищают от шлака, брызг и неровностей.
2.7.20. После окончания смены разрешается оставлять на ночь сварные стыки, сваренные одним заполняющим слоем, за исключением труб с толщиной стенки 14,1-17,0 мм, которые разрешается оставлять сваренными в соответствии с примечанием (**) табл.26.
2.7.21. Подготовку к сборке при сварке на внутренней технологической подкладке необходимо осуществлять так же, как при сварке по ручной подварке. Наружное и внутреннее усиления продольного (спирального) шва должны быть сняты до 0-0,5 мм на расстоянии не менее 25 мм от кромки.
2.7.22. Неровности на кромках должны быть в пределах, обеспечивающих прилегание технологической подкладки к внутренней поверхности трубы.
2.7.23. При сборке труб на технологической подкладке смещение кромок внутри трубопровода должно быть не более 3 мм. Конструкция внутренней технологической подкладки должна обеспечивать при данной величине смещения зазор между подкладкой и внутренними поверхностями свариваемых труб, а также между элементами самой подкладки не более 1 мм. Допускается местный зазор между подкладкой и внутренними поверхностями труб до 1,5 мм на длине не более 150 мм.
2.7.24. К сборке допускаются трубы как с заводской разделкой кромок, так и обрезанные газовой резкой. Допускается изменение разделки для сокращения ее поперечного сечения.
2.7.25. Автоматическую сварку корневого слоя порошковой проволокой осуществляют без предварительного подогрева. При наличии на поверхности трубы влаги стык подлежит просушке нагревом торцов до 50-100°С.
2.7.26. На поверхности технологической подкладки, прилегающей к поверхности трубы, должна быть канавка по форме внутреннего усиления. Технологическую подкладку устанавливают симметрично оси стыка (допускаемая асимметрия ±1,0 мм). Рабочая поверхность элементов подкладки должна быть очищена от масла и других загрязнений.
2.7.27. Технологический зазор между кромками, имеющими притупление 1,8 ±0,8 мм, должен составлять 2,5-3,0 в потолочной части стыка и 3,5-4,0 мм в верхней части стыка.
2.7.28. Сборку труб осуществляют с помощью прихватки, которая выполняется электродами с основным видом покрытия. Прихватку осуществляют с полным проваром корня в потолочном положении и используют в качестве дна плавильного пространства при начале автоматической сварки.
2.7.29. Автоматическую сварку корневого шва осуществляют порошковой проволокой ПП-АН19 и ПП-АН30 диаметром 2,4 мм. Толщина корневого слоя должна быть в соответствии с табл.26 (не менее) и обеспечиваться выступом формирующего ползуна соответствующей высоты. Сварку корневого слоя осуществляют на токе 280-300 А при напряжении на дуге 26-27 В.
2.7.30. Автоматическую сварку порошковой проволкой последующих слоев выполняют в соответствии с указаниями пп.2.7.12-2.7.18.
2.8. Автоматическая электродуговая сварка труб в среде защитных газов
2.8.1. Автоматическую сварку в среде защитных газов неповоротных стыков труб диаметром 1020-1420 мм необходимо выполнять на установках для двусторонней сварки.
Автоматическая сварка в защитных газах включает следующие основные операции:
подготовку труб в соответствии с подразд.2.2 настоящих ВСН;
механическую обработку торцов труб (см. рис.1);
сборку и сварку внутреннего и наружного корневых слоев;
осмотр внутреннего корневого шва и ручную дуговую сварку неудовлетворительно сформированных участков;
сварку заполняющих слоев шва;
подогрев перед сваркой облицовочного слоя;
сварку облицовочного слоя шва;
осмотр шва и ручную дуговую сварку неудовлетворительно сформированных участков.
2.8.2. Для повышения устойчивости горения дуги и стабильности процесса сварку внутреннего корневого слоя шва следует выполнять в смеси углекислого газа с аргоном.
2.8.3. Свободный торец нитки трубопровода должен быть закрыт инвентарной заглушкой, чтобы предотвратить сдувание струи газа (при внутренней сварке).
2.8.4. Сварку всех наружных слоев шва следует выполнять только в условиях, при которых исключено попадание осадков на стык и обеспечена защита от ветра.
2.8.5. При газоэлектрической сварке внутреннего и наружного корневого слоев неповоротных стыков труб производят автоматическую сварку наружного корневого слоя, которую начинают после того, как внутренними головками будет заварено по 200 мм корневого слоя шва на соответствующем полупериметре.
2.8.6. Сварку наружного корневого слоя шва необходимо начать не позднее чем через 5 мин после начала сварки внутреннего корневого шва на соответствующем полупериметре трубы.
При вынужденном перерыве сварки наружного корневого слоя необходим подогрев стыка до 150-200°С, а далее следует поддерживать эту температуру до возобновления процесса сварки.
2.8.7. Сварку всех наружных слоев шва выполняют одновременно двумя автоматами в направлении сверху-вниз.
2.8.8. Укладку конца трубы на лежку и перемещение центратора на очередную позицию сборки разрешается осуществлять только после окончания сварки наружного корневого слоя.
Для прохода сварочной головки высота лежек должна обеспечивать расстояние не менее 600 мм от надира трубы до поверхности грунта.
2.8.9. Перед сваркой облицовочного слоя на трубах с эквивалентом углерода более 0,40% необходим подогрев стыка наружным кольцевым подогревателем до температуры 220-250°С.
2.8.10. Экранирующее устройство для предохранения направляющего пояса от воздействия пламени следует установить перед подогревом стыка.
Газовые горелки должны быть установлены на расстоянии 50-70 мм от стыка на трубе, свободной от направляющего пояса.
2.8.11. Режимы сварки всех слоев шва для труб диаметром 1420 мм с толщиной стенки 15,7 мм приведены в табл.30.
Таблица 30
Параметры режима сварки | Наименование слоя |
| внутренний корневой | наружный корневой | заполняющие | облицо- вочный |
| | | первый | второй | третий | |
1 | 2 | 3 | 4 | 5 | 6 | 7 |
Скорость сварки, см/мин | 60-75 | 75-125 | 30-40 | 30-40 | 30-40 | 25-35 |
Сварочный ток, А | 190-210 | 220-240 | 220-240 | 190-210 | 180-200 | 170-190 |
Напряжение, В | 20-22 | 24-25 | .23-24 | 21-22 | 21-22 | 19-21 |
Частота колебаний электрода, мин | - | - | 130-150 | 110-130 | 110-130 | 110-130 |
Вылет электродной проволоки, мм | 9 | 9 | 12 | 10 | 10 | 10 |
Состав защитной газовой среды,%: | | | | | | |
аргон | 25-75 | 0 | 0 | 0 | 0 | 0 |
углекислый газ | 25-75 | 100 | 100 | 100 | 100 | 100 |
Расход газовой среды, л/мин | 30 | 30 | 40 | 40 | 40 | 30 |
Примечание. При сварке труб с большей толщиной стенки режимы сварки четвертого и последующих заполняющих слоев выбирают в соответствии с гр.6 настоящей таблицы.
2.8.12. Число заполняющих слоев в зависимости от толщины стенки трубы указано в табл.31.
Таблица 31
Толщина стенки трубы, мм | Число заполняющих слоев |
До 13 включительно | 2 |
Свыше 13 до 16, 5 включительно | 3 |
Свыше 16,5 до 19,5 включительно | 4 |
Свыше 19,5 до 26 включительно | 5-6 |
2.8.13. Амплитуду колебаний при сварке облицовочного шва выбирают из расчета перекрытия швом разделки по ширине на 1,5-2,0 мм в каждую сторону.
2.8.14. После сварки каждого слоя обязательна зачистка его поверхности металлическими щетками от шлака и брызг. В необходимых случаях потолочный участок наружных слоев шва обрабатывают абразивными кругами, чтобы получить ровную подложку для сварки последующих слоев.
2.8.15. Сварку в среде защитных газов ведут на постоянном токе обратной полярности.
2.8.16. Скорость подачи электродной проволоки (см/с) диаметром (см), с вылетом (см) для данных значений тока (А) электродной проволоки определяют по формуле
2.8.17. Перекрытия участков внутреннего корневого шва, сваренных внутренними сварочными головками, должны составлять на вертикальных и нижнем участках 20-40 мм. Перекрытие участков внутреннего корневого шва в потолочной части стыка не должно превышать 1 мм.
2.8.18. Рекомендуемая последовательность работы сварочных автоматов при наложении каждого слоя и расположение замков приведены на рис.9.
Рис.9. Последовательность наложения слоев при работе сварочных автоматов:
Н - наружный корневой слой;
В - внутренний корневой слой;
Зап - заполняющий слой; Обл - облицовочный слой (цифра после обозначения слоя указывает на очередность сварки данного участка в пределах слоя); - направление сварки
2.8.19. Места замков на наружных слоях должны быть смещены один относительно другого не менее чем на 15 мм.
2.8.20. Режимы сварки внутреннего корневого слоя шва обеспечивают получение внутреннего валика шириной 5-10 мм с усилением 0-3 мм.
2.8.21. Усиление облицовочного слоя шва должно быть в пределах 1-3 мм.
Допускается ослабление облицовочного шва на вертикальных участках в виде "седловины". Ослабление шва в центре "седловины" не должно быть ниже поверхности трубы.
2.8.22. Ширина облицовочного шва должна соответствовать данным, приведенным в табл.32.
Таблица 32
Толщина стенки трубы, мм | Ширина облицовочного шва, мм, не менее |
От 10,0 до 14,0 | 10,0 |
Свыше 14,0 до 17,0 | 11,0 |
Свыше 17,0 до 20,0 | 13,0 |
2.9. Специальные сварочные работы
2.9.1. Все специальные сварочные работы, а также ручная дуговая сварка на КС и НС производятся электродами только с основным видом покрытия. Если нет деталей заводского изготовления (отводов, тройников, переходов), в исключительных случаях и при соответствующем указании в проекте допускается монтажным организациям изготавливать эти детали в условиях, тождественных заводским, и при строгом соблюдении требований проекта и стандартов. Применяемые трубы и материал укрепляющих накладок должны соответствовать проекту и требованиям СНиП 2.05.06-85.
2.9.2. Изготовление деталей должно производиться с выполнением требований пп.13.18-13.23 СНиП 2.05.06-85.
2.9.3. Прихватку и сварку осуществляют электродами с основным видом покрытия или проволокой сплошного сечения в среде защитного газа.
2.9.4. Основным способом нагрева при термической обработке стыков труб диаметром 108 мм и более с толщиной стенки 16 мм и более должен быть индукционный нагрев токами промышленной (50Гц) или повышенной частоты. Для нагрева труб можно применять также гибкие пальцевые электронагреватели (ГЭН) или электронагреватели комбинированного действия (КЭН).
Сварное соединение должно быть подвергнуто термообработке непосредственно после сварки.
2.9.5. При проведении термической обработки следует руководствоваться ОСТ 36-50-86/Минмонтажспецстрой СССР "Трубопроводы стальные технологические. Термическая обработка сварных соединений. Типовой технологический процесс".
2.9.6. К работам по термической обработке сварных соединений следует допускать термистов-операторов, имеющих квалификацию не ниже 4-го разряда и удостоверение об окончании курсов по специальности термистов-операторов по термической обработке сварных соединений на монтаже.
2.9.7. Для углеродистой стали с нормативным временным сопротивлением разрыву до 490 МПа, низколегированной стали - 490-588 МПа режим термической обработки (высокий отпуск) должен быть следующим:
температура нагрева 550-580°С;
скорость нагрева 250°С/ч;
время выдержки 2 мин на 1 мм, но не менее 30 мин;
условия охлаждения - с печью или нагревателем со скоростью не выше 200 до 300°С/ч, далее на воздухе.
2.9.8. Контроль качества термической обработки следует выполнять измерением твердости металла во всех зонах сварного соединения с помощью переносных приборов. Уровень твердости должен находиться в пределах:
140-180 НВ - для углеродистой стали с нормативным временным сопротивлением разрыву до 490-539 МПа (50 кгс/мм );
160-200 НВ - для низколегированной стали с нормативным временным сопротивлением разрыву 490-539 МПа (50-55 кгс/мм );
190-220 НВ - для низколегированной стали повышенной прочности с нормативным временным сопротивлением разрыву свыше 539 МПа (55 кгс/мм ).
2.9.9. Ремонт сварного шва должен быть осуществлен до его термической обработки. В случае выполнения ремонта сварного шва после термической обработки следует повторить термическую обработку всего сварного шва.
2.9.10. Заварка технологических отверстий в трубах на стадии строительства трубопроводов
2.9.10.1. Перед началом производства работ с учетом конкретной марки, типа трубной стали и диаметра трубопровода в проекте производства работ (ППР) должны быть выбраны место и схема вырезки и заварки технологических отверстий по согласованию с заказчиком. Решение о необходимости выполнения указанных работ принимается при выполнении огневых работ.
2.9.10.2. Для труб с нормативным пределом прочности до 577 МПа (55 кгс/мм ), толщиной стенки до 12 мм заварка технологических отверстий может осуществляться путем вварки заплат. Форма, размеры и ориентация отверстий и заплат в этом случае должны соответствовать рис.10.
Рис.10. Форма и ориентация отверстия, заплаты и подкладного кольца и схема разделки кромок под сварку: - радиус отверстия в трубе; - радиус заплаты; - радиус подкладного кольца
2.9.10.3. Для труб с нормативным значением предела прочности 539 МПа (55 кгс/мм ) и выше, толщиной стенки 12 мм и более заварка технологических отверстий должна производиться путем вварки в трубу патрубка с эллиптическим днищем (заглушкой) (рис.11). Допускается вварка патрубка для герметизации отверстий в трубах с нормативным пределом прочности до 55 кгс/мм и с толщиной стенки до 12 мм.
Рис.11. Схема подготовки под сварку при заделке технологических отверстий с помощью патрубков
2.9.10.4. Технологические отверстия для последующей герметизации за счет вварки патрубков или заплат в ППР следует предусматривать, как правило, в верхней части периметра труб с допустимым смещением от зенита до 30°. Отверстия выполняются по шаблону газовой резкой.
Торцы отверстия в основной трубе при последующей вварке в него заплат обрабатываются механическим способом в соответствии с данными, приведенными на рис.10.
Торцы отверстия в основной трубе при последующей приварке к ней патрубка следует зачищать механическим способом для ликвидации острых краев.
Перед засыпкой трубопровода необходима установка бетонных колец, предохраняющих патрубок от механических повреждений.
2.9.10.5. Вырезку технологических отверстий в основной трубе в случае последующей вварки патрубков следует осуществлять таким образом, чтобы отверстие было на 10-15 мм меньше внутреннего диаметра патрубка.
2.9.10.6. Место вырезки технологического отверстия должно находиться на расстоянии не менее 250 мм от заводского или кольцевого сварного шва.
2.9.10.7. Заплаты следует изготавливать, как правило, заранее в стационарных условиях из отдельного участка трубы тех же диаметров, толщины стенки и класса прочности стали, что и основная труба. Размеры заплат не должны превышать 250х350 мм и быть меньше 100х150 мм. Разница между шириной и длиной заплаты должна быть не менее 50 мм. устанавливают в зависимости от длины и ширины заплаты. Кромки заплаты должны быть обработаны (зачищены) механическим способом и по форме и размерам соответствовать данным рис.10.
2.9.10.8. Патрубки должны быть изготовлены заранее из труб диаметром не выше 0,3 от диаметра основной трубы, но не более 325 мм, с толщиной стенки не более 16 мм. Максимальный размер патрубка для конкретной трубы определяется при условии установки резинового шара. Конструктивное и материальное исполнение врезок патрубков должно соответствовать требованиям ВСН 1-84/Мингазпром "Тройники и тройниковые соединения из стальных труб 5,5 и 7,5 МПа (55 и 75 кгс/мм )". Днища должны соответствовать ГОСТ 17379-83.
Толщина стенок свариваемых патрубков и заглушки должна быть одинакова.
2.9.10.9. Торец ввариваемого патрубка должен быть обрезан по шаблону и иметь разделку кромок 50° с притуплением 1,5-2,0 мм. Торец патрубка, привариваемого к днищу, должен быть подготовлен механическим способом с углом разделки кромок 30° (см. рис.11).
2.9.10.10. Технологические подкладки и подкладные кольца изготавливают из низкоуглеродистой стали (например, ВСт2, Ст10 и т.п.) толщиной 2-3 мм.
Диаметр подкладки 300-310 мм, диаметр отверстия 5-6 мм.
2.9.10.11. Перед прихваткой и сваркой внутренняя полость трубы в месте производства работ должна быть освобождена от воды и грязи. Прихватка и вварка подкладных колец, технологических подкладок, заплат и патрубков допускается только при положительных температурах металлов трубы и патрубка.
Температура предварительного подогрева должна соответствовать требованиям подразд.2.2 настоящих ВСН.
Специальные подогреватели должны обеспечивать равномерный подогрев места вварки заплат или патрубка.
Если подогрев по условиям сварки не требуется, при температуре окружающего воздуха +5°С и ниже необходимо произвести просушку участка трубы с технологическим отверстием.
2.9.10.12. При сборке заплаты рекомендуется вначале к заплате прихватить подкладное кольцо, затем заплата с подкладным кольцом должна быть поставлена в отверстие, прихвачена и приварена сплошным швом.
Величина смещения кромок заплаты по отношению к трубе не должна превышать 1,5 мм. Для удобства сборки допускается прихватка к свариваемым торцам временных технологических кронштейнов (см. рис.10) из электродных стержней, которые должны быть удалены механическим путем после прихватки заплаты.
2.9.10.13. При вварке патрубка с использованием технологической подкладки первоначально следует разметить отверстие, вставить одну половину подкладки и прихватить, вставить вторую половину подкладки, прихватить, а затем проварить сплошным швом по периметру технологического отверстия и стыку подкладки, оставив центральное отверстие подкладки свободным.
При сборке допускается использовать проволочные кронштейны.
Центральное отверстие следует загерметизировать, например, глиной, но таким образом, чтобы при подъеме давления в основной трубе до рабочего произошла разгерметизация отверстия.
2.9.10.14. Сварочно-монтажные работы по вварке заплат и патрубков следует производить за один рабочий цикл без перерывов до полного завершения облицовочного шва.
Температура предыдущего слоя перед наложением последующего слоя шва должна быть не ниже +100°С.
Если температура между слоями опустилась ниже +100°С, следует произвести подогрев на 100-150°С.
Отдельные слои шва должны выполняться в последовательности, указанной на рис.12.
Рис.12. Последовательность выполнения отдельных слоев шва при вварке заплат (I) и патрубков (II) (четырьмя участками протяженностью 100-250 мм каждый):
а - сварка нечетных слоев;
б - сварка четных слоев;
Н - начало сварки;
К - конец сварки
2.9.10.15. Приварку патрубков следует осуществлять не менее чем в три слоя с подваркой изнутри трубы, а облицовочный слой шва рекомендуется выполнять двумя валиками с последующей зачисткой шлифмашинкой.
2.9.10.16. Сварка должна производиться электродами с основным видом покрытия, рекомендованными разделом 2.3 настоящих ВСН для основной трубы данной категории прочности. Сварку заполняющих слоев шва целесообразно производить электродами диаметром 3,0-3,25 мм. При этом могут быть использованы электроды той же категории прочности, что и рекомендованные для сварки корневого слоя шва.
2.9.10.17. После приварки патрубков необходимо проводение отпуска с нагревом сварного соединения до 200°С и последующим охлаждением под теплоизолирующим поясом до полного остывания.
В случае вварки заплат последующий подогрев не производится, но место ремонта укрывается теплоизолирующим поясом. В процессе охлаждения как в первом, так и во втором случае попадание влаги на сварное соединение не допускается.
2.9.10.18. Последней операцией при вварке патрубка является прихватка и приварка эллиптической заглушки к патрубку.
Заглушка должна быть прихвачена и приварена не менее чем в 3 слоя сплошным швом к патрубку электродами с основным видом покрытия диаметром 2,5-3,25 мм, рекомендованными для сварки корневого слоя шва (см. табл.10). Перед сваркой торцы патрубка и заглушки необходимо просушить.
2.9.10.19. Сварные швы должны быть проконтролированы и радиографическим способом и ультразвуковым. Непровары в сварном соединении не допускаются. Контроль УЗК следует осуществлять как со стороны трубы, так и со стороны патрубка. Допустимые дефекты (кроме непроваров) должны соответствовать требованиям п.4.32 СНиП III-42-80.
2.9.10.20. При обнаружении недопустимых дефектов сварное соединение ремонту не подлежит. Участок трубы вырезается и на его место вваривается катушка длиной не менее диаметра основной трубы.
2.9.10.21. После окончания работ по вварке патрубка и заглушки составляется акт специальной формы (см. ВСН 012-88/Миннефтегазстрой "Формы исполнительной документации и правила ее оформления", ч.II).
2.9.11. Сварка прямых врезок
2.9.11.1. Приварка свечей пылеуловителей, вварка байпасов и других врезок должны быть выполнены через тройники заводского изготовления. Если предусмотрено проектом, допускаются прямые врезки при условии, что диаметр ответвления не превышает 0,3 диаметра основной трубы. Если диаметр ответвления превышает 0,3 диаметра основной трубы, следует применять только специальные детали трубопроводов.
2.9.11.2. Для выполнения прямой врезки в основной трубе по шаблону вырезают отверстие и после его обработки механическим способом присоединяют ответвление. Конструкция ответвления должна соответствовать ВСН 1-84/Мингазпром.
2.9.11.3. При выполнении прямых врезок условия подогрева и технология их вварки (тип сварочных материалов, количество слоев шва и т.д.) должны соответствовать в основном требованиям раздела 2.9.10.
2.9.12. Сварка захлестов
2.9.12.1. В зависимости от конкретных условий различают следующие виды технологических захлестов:
концы трубопровода свободны (не засыпаны землей) и находятся в траншее или на ее бровке;
один конец трубопровода защемлен (засыпан, подходит к крановому узлу), а другой имеет свободное перемещение;
оба соединяемых конца трубопровода защемлены (соединены с патрубками запорной арматуры).
В первых двух случаях замыкание трубопровода можно осуществить сваркой одного кольцевого стыка - захлеста. В последнем случае необходима вварка катушки с выполнением двух кольцевых стыков (рис.13).
Рис.13. Схема ликвидации технологического разрыва:
а - при монтаже захлеста;
б - при врезке катушки;
1 - труба;
2 - катушка
2.9.12.2. Выполнять работы по ликвидации технологических разрывов следует, как правило, в дневное время при температуре окружающего воздуха не ниже -40°С.
2.9.12.3. Монтаж захлестов и катушек необходимо выполнять только в присутствии прораба или мастера с последующим составлением акта (см. ВСН 012-88/Миннефтегазстрой) . В акте указывают:
фамилии электросварщиков и схему их расстановки;
сварочные материалы и результаты визуального и радиографического контроля стыка.
2.9.12.4. Если трубопровод находится в траншее, в месте соединения труб необходимо подготовить приямок, размеры которого должны беспрепятственно обеспечивать работы по сварке, контролю и изоляции стыка.
2.9.12.5. Если соединяемые трубы были ранее изолированы, необходимо удалить изоляцию на расстоянии не менее 150 мм от места сварки.
2.9.12.6. Для сварки захлеста в траншее необходимо оставлять незасыпанным один из примыкающих участков трубопровода на расстоянии 60-80 м от места предполагаемого захлесточного стыка.
2.9.12.7. Подготовку труб к сборке с помощью центраторов при монтаже захлестов следует выполнять в приведенной последовательности:
один из концов трубопровода заранее подготавливают под сварку и укладывают на опоры высотой 50-60 см по оси трубопровода;
плеть, образующую другой конец трубопровода, вывешивают рядом с первой и делают разметку места реза. Разметка линии реза должна быть выполнена только с помощью шаблона, чтобы исключить образование косого стыка;
газовую резку плети следует проводить с последующей подготовкой фасок любым станком типа СПК. Как исключение (если нет станка типа СПК) допускается применять газовую резку (преимущественно механизированную) с последующей зачисткой абразивным инструментом;
стыковку труб с применением наружного центратора выполняют путем подъема обрезанной плети трубоукладчиками на высоту не более 1,5 м на расстоянии 60-80 м от конца трубы; при этом за счет упругих деформаций обрезанный конец провисает, что позволяет совместить один конец с другим;
не допускается стропить трубу для подъема в месте расположения сварных кольцевых швов;
регулировку зазора в стыке осуществляют изменением высоты подъема трубопровода трубоукладчиками.
2.9.12.8. Подготовку труб к сборке при врезке катушек осуществляют в приведенной последовательности:
концы труб, которые должны быть соединены, обрезают и подготавливают под сварку в соответствии с требованиями, изложенными в настоящем разделе;
катушку изготавливают требуемой длины на трубы той же толщины, того же диаметра и марки стали, что и соединяемые трубы;
трубоукладчиком пристыковывают катушку к трубопроводу, собирают стык с применением наружного центратора и сваривают первый стык. Сборку второго стыка выполняют с помощью наружного центратора после окончания сварки первого стыка;
длина катушки должна быть не менее одного диаметра трубы.
2.9.12.9. Для обеспечения требуемого зазора или соосности труб запрещается натягивать трубы, изгибать их силовыми механизмами или нагревать за пределами зоны сварного стыка, а также категорически запрещается вваривать любые присадки.
2.9.12.10. Сборка разнотолщинных труб при монтаже захлестов не допускается.
2.9.12.11. Прихватку следует выполнять электродами с основным видом покрытия, предназначенным для сварки корневого слоя шва.
2.9.12.12. Наложение прихваток и сварку труб диаметром более 426 мм должны выполнять без перерывов в работе не менее 2 электросварщиков одновременно.
2.9.12.13. Если сварщик может проникнуть внутрь трубы, он выполняет внутреннюю подварку стыка на нижней четверти периметра и в местах видимых дефектов электродами, предназначенными для сварки корневого слоя шва.
2.9.12.14. Сварные соединения захлестов оставлять незаконченными не разрешается.
2.9.13. Муфтовые сварные соединения
2.9.13.1. Муфтовые соединения разрешаются при сварке труб диаметром до 59 мм из стали марок Ст3, 10, 20 или из аналогичных им.
2.9.13.2. Конструкция сварного соединения должна соответствовать ГОСТ 16037-80 "Соединения сварные стальных трубопроводов, основные типы, конструктивные элементы и размеры".
2.9.13.3. Муфта должна быть изготовлена в соответствии с требованиями ГОСТ 16037-80 из труб соответствующих типоразмеров для обеспечения зазора между трубой и муфтой 1 ±0,5 мм и из стали аналогичного уровня класса прочности. Длина муфты должна быть не менее 50 мм (рис.14).
Рис.14. Размеры муфтового соединения
2.9.13.4. Сварку следует осуществлять на минимальных токах, регламентированных заводом-изготовителем и обозначенных на этикетках электродных пачек электродами с основным видом покрытия типа Э42А или Э50А, указанных в табл.10 настоящих ВСН.
2.9.13.5. Усиление должно быть не более 1 мм для соединений, выполненных в нижнем положении и не более 2 мм - в остальных положениях; ослабление - не более 2 мм во всех пространственных положениях.
2.9.13.6. Сварные швы не должны иметь видимых дефектов (подрезов, пор, незаплавленных кратеров, трещин).
2.9.13.7. При контроле допускных сварных соединений, а также при испытаниях электросварщиков следует испытывать муфтовые сварные соединения на растяжение и на сплющивание по ГОСТ 6996-66 (см. приложение 1).
Все муфтовые сварные соединения подвергаются контролю с применением цветной красящей дефектоскопии (ЦКД) по ОСТ 36-76-83. Дополнительно к 100%-ному контролю ЦКД 1% муфтовых сварных соединений в процессе сварки подвергается механическим испытаниям на растяжение и сплющивание. При этом для механических испытаний выбираются соединения, самые худшие по внешнему виду.
2.10. Ремонт сварных соединений
2.10.1. Ремонт сварных соединений, выполненных дуговой сваркой, производится в случаях, предусмотренных п.4.34 СНиП III-42-80 и приложением 2.
2.10.2. Ремонт участков сварных швов, имеющих дефекты, осуществляют путем их вышлифовки с помощью абразивных кругов с последующей заваркой ручной дуговой сваркой в соответствии с п.4.35 СНиП III-42-80.
Примечания: 1. Допускается удалять с помощью газовой резки или воздушно-дуговой строжки участки, имеющие дефекты, с последующей зачисткой мест реза абразивным инструментом.
2. Удаление участков сварных швов, имеющих дефекты, с помощью газовой или поверхностной воздушно-дуговой резки допускается только при длине участков не менее 200 мм и сварных соединений из сталей всех уровней прочности, кроме сталей термического упрочнения.
2.10.3. Если после ремонта по периметру стыка обнаружены неудаленные дефекты, разрешается их дополнительная вышлифовка с последующей заваркой. Повторный ремонт одного и того же дефекта не разрешается.
2.10.4. Ремонт сварных швов стыков труб диаметром до 1020 мм выполняют только снаружи, а труб диаметром 1020 мм и более - как снаружи, так и изнутри в зависимости от глубины залегания дефектов.
2.10.5. Ремонт сварных стыков труб диаметром 1020 мм и более снаружи трубы осуществляют, если недопустимые дефекты расположены в заполняющих и облицовочном слоях шва. Трубопровод ремонтируют изнутри, если недопустимые дефекты расположены в корневом слое шва, горячем проходе и подварочном слое шва и возможен доступ к месту ремонта. В случае вышлифовки дефектного участка трубы она должна вестись шлифовальной машинкой с напряжением не более 36 В. Место расположения дефекта определяет и отмечает дефектоскопист ПИЛа.
2.10.6. Места ремонта и номер ремонтируемого стыка трубы указываются несмываемой краской.
2.10.7. Разметку для последующей вышлифовки участков сварного шва с дефектами снаружи трубы выполняют таким образом, чтобы длина вышлифованных участков сварного шва превышала длину исправляемого дефектного участка не менее чем на 30 мм в каждую сторону.
2.10.8. Разметку участков сварного шва, имеющего дефекты изнутри трубы, проводят с помощью кольцевого шаблона с нанесенными делениями, которые соответствуют показаниям мерного пояса.
Как и при наружном ремонте, длина удаляемых участков сварного шва изнутри трубы должна превышать размеры исправляемого дефектного участка не менее чем на 30 мм в каждую сторону.
2.10.9. Разделка выбранных под сварку участков с дефектами должна соответствовать виду дефекта и обеспечивать качество выполнения сварочных работ.
Ширина выбранного участка сварного шва с дефектом зависит от толщины стенки свариваемых труб:
Толщина стенки трубы, мм | Ширина удаляемого участка, мм |
До 5 | До 8 |
Свыше 5-10 | 10-12 |
Более 10 | 13-20 |
Глубину выбранного участка определяют глубиной замеченного дефекта. Перед выполнением сварочных ремонтных работ следует в зоне сварки удалить ржавчину и влагу, а также следы изоляции.
2.10.10. Ремонт одного стыка разными сварщиками запрещается.
2.10.11. Все отремонтированные участки стыков должны быть подвергнуты внешнему осмотру, радиографическому контролю и удовлетворять требованиям п.4.32 СНиП III-42-80.
2.11. Сварка трубопроводов, транспортирующих сероводородсодержащие среды
2.11.1. Настоящие требования распространяются на производство сварочно-монтажных работ и термическую обработку стыков промысловых нефтегазопроводов, предназначенных для транспортировки сред с парциальным давлением сероводорода свыше 1 МПа, а содержанием сероводорода не выше 10% (объемных). Трубопроводы, сваренные в соответствии с требованиями настоящих ВСН, ингибируются, влажность транспортируемого газа не должна превышать 60%.
2.11.2. Сварку, сборку и контроль качества промысловых нефтегазопроводов, предназначенных для транспортировки сред с парциальным давлением сероводорода в диапазоне 0,3-1,0 МПа, следует проводить в соответствии с ВСН 005-88/Миннефтегазстрой "Строительство промысловых стальных трубопроводов. Технология и организация".
2.11.3. Контроль качества сварных соединений трубопроводов, транспортирующих сероводородсодержащие среды, включает:
сплошной операционный контроль в процессе сборки и сварки стыков;
осмотр и измерение геометрических параметров швов;
проверку качества шва физическими методами контроля;
механические испытания допускных стыков и контроль твердости металла шва и зоны термического влияния.
Все сварные стыки подвергаются 100%-ному радиографическому контролю до термообработки с дублированием 20% стыков ультразвуковым методом контроля для проверки на отсутствие трещин после термообработки.
Критерии оценки качества сварных соединений представлены в приложении 2 со следующими дополнительными ограничениями по результатам радиографического контроля:
в корне шва не должно быть непроваров, находящихся в пределах чувствительности снимка, регламентированной ГОСТ 7512-82;
в корне шва не должно быть утяжин (провисов) на длине более 12% периметра, глубиной свыше 10% толщины стенки (но не более 1,5 мм).
Контроль твердости сварных соединений выполняется в объеме 10% стыков методом "Польди" или другими аналогичными. Замеры проводятся в 3 точках: на металле шва, в зоне термического влияния (на расстоянии 2 мм от линии сплавления) и на основном металле (на расстоянии 50 мм от шва).
Величина твердости не должна превышать 220 единиц по шкале Бриннеля. Результаты контроля твердости записываются в журнал термической обработки стыков или оформляются актом и прилагаются к сварочному журналу.
2.11.4. Аттестацию электросварщиков перед допуском их к сварке трубопроводов, предназначенных для транспортировки сероводородсодержащих сред, следует осуществлять в соответствии с приложением 1.
2.11.5. Сварка трубопроводов для транспортировки сероводородсодержащих продуктов с парциальным давлением сероводорода свыше 1 МПа при содержании сероводорода не выше 10% (объемных) осуществляется с использованием ручной дуговой и автоматической сварки под флюсом.
2.11.6. Сварочно-монтажные работы разрешается выполнять при температуре окружающего воздуха не ниже -20°С. При скорости ветра свыше 10 м/с, а также при выпадении атмосферных осадков производить сварочные работы без инверторных укрытий запрещается.
2.11.7. По общим вопросам сборки и сварки и требованиям к сварочным материалам и металлу труб, не рассматриваемым в данном подразделе ВСН, следует руководствоваться СНиП III-42-80 "Магистральные трубопроводы", "Правилами производства и приемки работ" и предыдущими разделами настоящего ВСН.
2.11.8. График для определения парциального давления сероводорода в зависимости от его концентрации при различных рабочих давлениях в трубопроводе представлен в приложении 5.
2.11.9. Требования настоящего подраздела распространяются на сварку трубопроводов из низкоуглеродистых нелегированных сталей типа Ст20, 20ЮЧ и низколегированных сталей класса прочности не выше Х46, отвечающих требованиям ТУ 40-78/H S, ТУ 28-40/82- H S, ТУ SХ46SS-28/40-83. Конкретная марка стали указанных типов определяется проектом. Использовать трубы, не оговоренные проектом, можно только по согласованию с проектной организацией и заказчиком.
2.11.10. Запрещается применять трубы и детали трубопроводов, не имеющие сертификатов (заводских паспортов, подтверждающих их соответствие требованиям государственных стандартов или технических условий, товарного знака или маркировки).
2.11.11. Все детали трубопроводов и арматуры, контактирующие с коррозионно-активными средами, должны поставляться заказчиком в заводском исполнении. Допускается изготовление отдельных видов соединительных деталей (по согласованию с заказчиком) на промышленных базах строительно-монтажных подразделений при условии соблюдения всех требований СНиП 2.05.06-85 и настоящего раздела ВСН. Независимо от способа изготовления тройники, отводы и заглушки должны быть термообработаны по режиму, указанному в табл.33.
2.11.1.2. Концы труб должны иметь снятые фаски под углом 30-35° в соответствии с рис.1, а, б.
2.11.13. Сортамент электродов для ручной дуговой сварки должен соответствовать данным, приведенном в табл.33.
Таблица 33
Назначение | Вид электродного покрытия | Тип электродов по ГОСТ 9467-75 | Диаметр электродов, мм | Марка электродов |
Для сварки первого корневого слоя шва | Целлюлозный | Э42 | 3,0-4,0 | Фокс Цель Кобе-6010 Флитвелд-5П ВСЦ-4 Тиссен Цель 70 |
Для сварки второго слоя (горячего прохода) | Целлюлозный | Э50 | 3,25-4,0 | Фокс Цель Кобе-6010 ВСЦ-4 Фокс Цель-75 Тиссен Цель 70 |
Для сварки корневого слоя | Основной | Э50А | 2,0-3,25 | ЛБ-52У Фокс ЕВ50 Феникс К50Р Гарант УОНИ-13/55 ОЗС/ВНИИСТ-26 |
Для сварки заполняющих и облицовочных слоев | Основной | Э50А | 3,0-4,0 | ОЗС/ВНИИСТ-26 Фокс ЕВ50 Гарант УОНИ-13/55 ОК.48.30 |
Примечание. Для выполнения подварочного шва можно использовать любые электроды с основным покрытием, указанные в таблице.
2.11.14. Сортамент сварочных материалов для автоматической сварки под флюсом должен соответствовать данным табл.34.
Таблица 34
Назначение | Марка флюса | Марка проволоки |
Для сварки заполняющих, облицовочных и подварочных слоев | АН-348А | СВ-08ГА |
| | СВ-08АА |
| ФЦ-16 | СВ-08ГА |
| ВВ-25 | EMS 2 |
| LW330 | S 2 |
Примечание. Флюс ФЦ-16 используется только для сварки первого заполняющего слоя (для улучшения отделимости шлаковой корки) на трубах диаметром 1020 мм.
2.11.15. Разрешается применять сварочные материалы, не указанные в табл.33, 34, при условии положительных результатов испытаний на стойкость против сероводородного коррозионного растрескивания. Испытания на стойкость против сероводородного коррозионного растрескивания должны проводиться по методике МСКР-01-85 или NAСЕ ТМ-01-77. По результатам испытаний должно иметься заключение ВНИИСТа.
2.11.16. Транспортировка труб и секций волоком, а также их сбрасывание с транспортных средств запрещается.
2.11.17. Допустимое смещение кромок перед сваркой должно соответствовать п.2.2.3 настоящих ВСН.
2.11.18. Допускается ремонт отдельных участков с вмятинами, забоинами и задирами в соответствии со СНиП III-42-80.
Если необходим ремонт с использованием сварки, следует применять электроды с основным видом покрытия, указанные в табл.33.
Концы труб с недопустимыми дефектами следует обрезать газорезкой. После этого кромку труб необходимо зачищать до металлического блеска с последующим устранением неровностей на поверхности.
2.11.19. Ремонту не подлежат дефектные торцы запорной (распределительной) арматуры; арматура с дефектом должна быть заменена на новую.
2.11.20. Соединение разностенных труб и арматуры должно производиться в соответствии с пп.4.5 и 4.8 СНиП III-42-80.
2.11.21. Сборку труб с продольным швом следует производить так, чтобы продольные швы каждой трубы были смещены по отношению к швам смежных труб не менее чем на 100 мм (рис.15).
Рис.15. Схема сварки труб с продольным швом:
1 - продольные швы;
2 - кольцевой шов; - не менее 100 мм
2.11.22. Все свариваемые торцы труб на ширине не менее 150 мм просушиваются при температуре +50°С независимо от температуры окружающего воздуха, толщины стенки и диаметра трубы. Просушка не должна заменять предварительный подогрев.
2.11.23. Концы свариваемых труб и деталей трубопроводов должны подогреваться перед сваркой стыков труб основными электродами при температуре ниже +5°С до температуры 100-120°С.
2.11.24. При сварке корня шва и горячего прохода электродами целлюлозного типа при любой толщине стенки и любой температуре окружающей среды стыки подогреваются до температуры 150-200°С.
2.11.25. Подогревающее устройство должно обеспечить равномерный нагрев свариваемых труб по всему периметру. Температуру подогрева кромок можно контролировать контактными пирометрами, термокарандашами, обеспечивающими точность замера ±10%, прибором ТП-1 и др.
2.11.26. На всех технологических захлестах и прочих разрывах должны быть установлены заглушки, предотвращающие попадание влаги в трубу.
2.11.27. При необходимости следует делать селекцию и калибровку труб (см. приложение 3). При проведении калибровки торцы труб не должны быть выведены за пределы плюсовых допусков по наружному диаметру. Допускается калибровка бесшовных труб диаметром до 426 мм с нормативным значением предела текучести до 32 кгс/мм включительно. Перед калибровкой труб деформируемый участок должен быть нагрет до температуры +250°С.
2.11.28. Автоматическую дуговую сварку под слоем флюса следует применять для выполнения заполняющих и облицовочных слоев поворотных стыков труб диаметром 325 мм и выше. Для труб диаметром 1020 мм автоматической сваркой под флюсом разрешается выполнять также подварочные швы.
2.11.29. При ручной дуговой сварке ширина валика подварочного шва должна составлять 8-10 мм. Подварочные швы выполняются после первого корневого слоя. Запрещается подварка стыка после сварки заполняющих и облицовочных слоев.
Подварку поворотных стыков, а также стыков разностенных труб выполняют по всему периметру.
Подварку неповоротных стыков выполняют ручной дуговой сваркой и осуществляют на нижней четверти периметра и на участках стыка с непроваром.
2.11.30. При сварке стыков труб с толщиной стенки до 16,5 мм число слоев шва, выполненных автоматической сваркой под слоем флюса, должно быть не менее 2; при толщине 16,5-20,5 мм - не менее 3; при толщине 20,5-24,0 мм - не менее 4; при толщине 24,0-28,0 мм - не менее 5; при толщине 28,0-32,0 - не менее 6.
2.11.31. При сварке трубопроводов диаметром 530 мм и более предпочтительной схемой организации работ является монтаж нитки труб из 3-трубных секций укрупненной бригадой, работающей по поточно-групповому или поточно-расчлененному методу.
2.11.32. Сварку трубопроводов диаметром 720 мм и более рекомендуется выполнять двусторонней автоматической сваркой под флюсом на базах типа ПАУ. Порядок наложения слоев в этом случае должен быть следующий: первый - с наружной поверхности трубы, второй - изнутри трубы, третий и последующие до заполнения всей разделки кромок накладываются с наружной поверхности трубы.
2.11.33. Запрещается опускать не остывшие до температуры окружающего воздуха стыки на мокрый грунт или снег.
2.11.34. Запрещается прекращать сварку до полного заполнения разделки кромок.
2.11.35. Каждый слой шва перед наложением последующего, а также прихватки необходимо тщательно очищать от шлака до металлического блеска (шлифмашинкой, щеткой и т.д.).
2.11.36. Запрещается зажигать дугу вне шва на трубе.
2.11.37. При сварке корневых слоев целлюлозными электродами время между первым слоем и горячим проходом не должно превышать 5 мин. Время между первым и вторым слоем при сварке корневых слоев электродами с основным покрытием также не должно превышать 5 мин. При выполнении последующих слоев время между слоями должно быть не более 10-12 мин.
2.11.38. Стыки с выявленными при контроле дефектами могут быть исправлены, если их суммарная длина не превышает 10% периметра. Стыки с трещинами ремонту не подлежат и должны быть вырезаны.
2.11.39. Выполнять ремонт стыков сваркой изнутри трубы не допускается. Дефектное место шва удаляют абразивным инструментом, допускается также его удаление газовым резаком с последующей обработкой поверхности реза до металлического блеска шлифмашинкой.
2.11.40. Заваривать ремонтные участки шва необходимо электродами с основным покрытием диаметром 2,5-3,25 мм в соответствии с табл.33. Предварительный подогрев при этом должен выполняться до +150°С при любой температуре окружающего воздуха.
2.11.41. Контроль отремонтированных участков стыков должен производиться после термообработки радиографическим методом и замерами твердости и удовлетворять требованиям настоящего документа. Результаты контроля качества отремонтированных стыков с соответствующим заключением должны записываться в исполнительную документацию.
2.11.42. Повторный ремонт сварных швов не допускается.
2.11.43. Термической обработке подлежат все сварные стыки трубопроводов, предназначенных для транспортировки продуктов, содержащих сероводород с парциальным давлением свыше 1 МПа, независимо от толщины стенки трубы и величины эквивалента углерода металла трубы.
2.11.44. Техническое руководство по термической обработке осуществляет руководитель монтажного участка. К проведению работ по термообработке сварных стыков могут быть допущены лица, прошедшие обучение по специальной программе и имеющие удостоверение термиста-оператора соответствующего разряда.
2.11.45. В обязанности бригады входит подготовка стыков к термообработке, установка и подключение нагревателей и термопар, регулировка и контроль режимов, оформление исполнительной документации. Оператор несет ответственность за качество выполненной им термообработки сварного соединения.
2.11.46. Источник питания и другое электрооборудование на участке термообработки обслуживает электрик, подчиняющийся руководителю работ по термообработке.
Обслуживание электронных потенциометров и пирометрических приборов, их систематическую проверку и наладку осуществляют специалисты по КИПу.
2.11.47. Режим термической обработки стыков трубопроводов приведен в табл.35.
Таблица 35
Материал | Температура нагрева, °С | Выдержка при максимальной температуре, мин | Скорость нагрева, °С/ч | Скорость* охлаждения, °С/ч до +300°С |
Низкоуглеродистые нелегированные стали типа сталь 20 и сталь 20ЮЧ | 600 | 60 | 600 | 600 |
Низколегированные стали ТУ SХ46SS-28/40-83 ТУ 28-40/82-НS ТУ 40-78/НS | 550 | 60 | 600 | 600 |
Охлаждение ниже +300°С не контролируется и может выполняться либо с печью, либо на спокойном воздухе.
2.11.48. Стыки трубопроводов из низкоуглородистых нелегированных сталей диаметром 108 мм и меньше, имеющих толщину стенки 6 мм и меньше, могут быть термически обработаны по сокращенному режиму: температура нагрева 660 °С, выдержка при 660°С - 30 мин, скорость нагрева 600°С/ч, охлаждение совместно с печью до 300°С, далее на воздухе.
2.11.49. Термическая обработка сварных стыков труб, регистрация и регулирование температуры должны производиться в соответствии с заданным режимом по установленной программе. Класс точности регистрирующих самопишущих приборов должен быть не ниже 1. Диаграммы сохраняют в монтажной организации. К исполнительной документации прикладывают сертификат термической обработки сварных стыков.
2.11.50. В случае нарушения термической обработки в сторону недогрева стык проходит повторно термическую обработку, в случае перегрева стык бракуется; при этом выявляется причина отклонения от режима и устраняется.
Общее число повторных термических обработок должно быть не более 3, после чего стык бракуется.
2.11.51. Для контроля температуры при термической обработке сварных стыков должны быть применены хромель-алюмелевые термопары.
Все новые термопары должны подвергаться проверке при температуре, соответствующей температуре термообработки стыков на специальном стенде по эталонному комплекту ("термопара-прибор"). Эталонный комплект должен иметь паспорт госпроверки.
2.11.52. Рабочий (горячий) спай термопар должен быть сварен. Число витков скрутки рабочего спая должно быть не более 3.
Использование термопар с незаваренными концами ("скрутками") и с разбитым шариком не допускается. Проводники термопары должны быть изолированы друг от друга керамическими бусами или переплетены шнуром асбеста.
До установки на рабочее место термопары должны быть проверены. Проверка рабочего спая может осуществляться методом "горячей спички". Свободные концы термопары подключают к потенциометру или милливольтметру, а рабочий спай термопары нагревают пламенем спички. При правильном подключении термопары прибор должен показать температуру горячего спая порядка 400-450°С (для хромель-алюмелевой термопары). Если стрелка прибора отклоняется в обратную сторону, концы термопары следует пересоединить и вторично сделать проверку.
Неподвижность стрелки прибора при проверке означает, что термопара для замера непригодна, так как состоит из одинаковых проводников (хромель + хромель или алюмель + алюмель).
2.11.53. Число термопар, устанавливаемых на стык, должно быть следующим:
при питании элемента нагревателя от одного источника
для труб диаметром до 325 мм (включительно) одну термопару устанавливают в зените стыка;
для труб диаметром от 325 до 426 мм (включительно) одну термопару устанавливают в нижней (потолочной) части стыка;
для труб диаметром более 426 мм устанавливают две термопары: одну в верхней, другую - в нижней части стыка;
при питании элемента нагревателя от нескольких источников термопары устанавливают в центре каждого элемента (секции).
При термообработке стыка, имеющего разную толщину стенки свариваемых труб, термопару (термопары) устанавливают со стороны толстостенной трубы.
2.11.54. При термообработке кольцевых стыков муфельными нагревателями термопара располагается по образующей трубы (рис.16); при термообработке индукционным способом и замере температуры с помощью потенциометров термопару следует установить перпендикулярно к оси трубы, а электроды бифилярно скрутить. Такое положение электродов термопары используется для уменьшения наводок индукционного поля нагревателей на измерительную цепь потенциометра.
Рис.16. Расположение термопар на стыках при нагреве муфельными печами или электрическими элементами сопротивления:
1 - сварной шов;
2 - горячий слой термопары;
3 - электроды термопары;
4 - устройство для крепления термопары;
5 - асбест
2.11.55. Термопара крепится на трубе, подгибаемой скобкой на расстоянии 15-20 мм от края сварного шва (рис.17).
2.11.56. При термической обработке участки термопары, расположенные в зоне нагрева, должны быть защищены асбестом от непосредственного воздействия источника тепла. Длина нагреваемого участка термопары в области высоких температур не должна превышать 150 мм.
Термопары необходимо устанавливать так, чтобы их свободные концы (холодный спай) не подвергались нагреву выше температуры окружающего воздуха, чтобы не вызвать неправильные показания прибора.
2.11.57. Специализированные организации проводят госпроверку контрольно-измерительных приборов согласно требованиям, оговоренным в паспорте на прибор.
Точность показаний электронного потенциометра проверяют не реже одного раза в неделю и после транспортировки поста на дальнее расстояние (транспортировка, не связанная с передвижением поста от стыка к стыку в процессе термообработки).
Результаты проверки заносят в участковый журнал проверки приборов КИП.
2.11.58. Все приборы, регистрирующие и регулирующие термообработку, должны эксплуатироваться в соответствии с паспортными данными.
2.11.59. Подключать термопары к приборам следует с помощью компенсационных проводов. Тип компенсационного провода должен соответствовать типу термопары.
Соединение термопар с потенциометром медным проводом не допускается, так как это может привести к неправильным показаниям прибора.
2.11.60. При подключении компенсационных проводов к термопаре и к прибору следует соблюдать полярность, т.е. соединять потенциалы одного знака - плюс с плюсом, минус с минусом. Положительным потенциалом обладает хромель, отрицательным - алюмель. Хромель в отличие от алюмеля не притягивается магнитом. На приборе в месте подключения компенсационного провода на контактной колодочке обязательно должны быть поставлены знаки плюс и минус.
Соединение термопары с компенсационным проводом должно выполняться надежными контактами - винтовыми соединениями или соединительными разъемами, обеспечивающими хороший контакт. Металлические неизолированные соединительные колодки не должны соприкасаться. "Скрутки" не допускаются.
Компенсационные провода необходимо по возможности прокладывать перпендикулярно токоведущим проводам (сварочным электропроводам) при замере температуры с целью снижения воздействия магнитных полей на показание приборов. Поскольку потенциометры рассчитаны на прием ЭДС при сопротивлении внешней цепи до 200 Ом, в условиях монтажа допускается использование компенсационного провода, сопротивление которого не превышает входного сопротивления прибора.
2.11.61. Для обеспечения надежной работы измерительной схемы и уменьшения наводок от магнитных полей между мощными источниками электромагнитных полей и приборами, расположенными на расстоянии менее 10 м, должны быть установлены экраны.
2.11.62. Термическую обработку сварных соединений трубопроводов различного назначения в полевых условиях предпочтительно проводить с использованием оборудования для термообработки ОТС-121, ОТС-62 и термометрической лаборатории ЛТП-1. Места вварки бобышек диаметром 20-80 мм должны термообрабатываться нагревателями типа НБ-721.
2.11.63. Термическая обработка сварных соединений может производиться нагревателями, обеспечивающими зону равномерного нагрева 70-100 мм (например, электрическими муфельными печами типа ПТО, элементами сопротивления).
2.11.64. Термообработку сварных стыков трубопроводов диаметром 57 мм и меньше допускается производить пламенем газовой горелки. Для равномерного распределения пламени по всей окружности стыка на трубу надевают стальную или асбестовую воронку (рис.18). Замерять температуру можно термокраской или термокарандашами через каждые 15 мин, о чем производится запись в специальном журнале и заполняется сертификат.
Рис.18. Нагрев стыка сварочной горелкой:
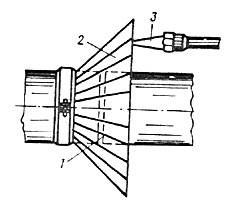
1 - сварочный шов;
2 - стальная или асбестовая воронка;
3 - горелка
2.11.65. Термообработку стыков трубопроводов диаметром 114 мм и меньше разрешается производить при групповом подключении гибких элементов (от одного источника питания). Групповое подключение может быть допущено только при следующем условии: одновременно обрабатываемые стыки должны иметь одинаковые диаметр и толщину стенки труб.
2.11.66. Перед применением новые нагреватели или нагреватели, полученные из ремонта, следует проверить на специальном стенде, чтобы определить равномерность температурного поля и потребляемую мощность, а результаты записать в журнал проверки. Повторную проверку нагревателей в процессе производства следует проводить:
для вновь поступивших с завода нагревателей - через первые 75 циклов термообработки, далее - через каждые 50 циклов;
для отремонтированных нагревателей - через 50 циклов термообработки.
2.11.67. При установке нагревателей на сварном стыке необходимо тщательно изолировать места возможного отвода тепла:
при нагреве муфельными нагревателями следует изолировать трубу асбестовыми матами на длине около 400 мм в каждую сторону от нагрева;
При нагреве гибкими пальчиковыми нагревателями необходимо изолировать стык вместе с нагревательными элементами асбестовыми матами суммарной толщиной не менее 40-50 мм на длине 800 мм (по 400 мм от шва);
места приварки фланцев и т.п. должны быть изолированы на ту ширину, которую позволяют габариты фланцев, отводов и т.п.
2.11.68. Во время термообработки до снятия нагревателя со стыка концы труб следует заглушать с торцов, чтобы предотвратить интенсивное охлаждение сварных стыков трубопроводов за счет циркуляции воздуха внутри трубы.
2.11.69. Техническое состояние и исправность оборудования поста термообработки необходимо проверить перед проведением термической обработки.
2.11.70. Термическую обработку сварных стыков трубопроводов следует проводить по возможности непосредственно после окончании сварки.
2.11.71. При термообработке сварных соединений необходимо принять меры для предотвращения их деформации под влиянием температурного расширения и массы трубы. Деформация сварных соединений наиболее вероятна при расположении трубопровода на склонах, переходах через овраги, на углах поворота, в узлах, создающих жесткий контур на участках трубопровода, не вписывающихся в рельеф местности. Для исключении деформации трубопровода в местах сварных соединений необходимо предусмотреть выравнивание грунта под трубой, вставку вертикальных кривых на спусках, подъемах, переходах через овраги, установку опор в местах резкого изменения рельефа, а также на прямолинейных участках, где можно ожидать провисания труб.Для проведения термической обработки стыков трубопроводов на монтажных площадках межтрубное пространство должно быть не менее 250 мм.
2.11.72. Для устранения изгиба при термообработке на стеллаже необходимо устанавливать трехтрубную секцию так, чтобы каждая из труб лежала не менее чем на двух опорах, расположенных на расстоянии 2,5-3,0 м с каждой стороны от середины трубы.
2.11.73. При завершении цикла термообработки необходимо отключить силовую цепь и контрольно-измерительную аппаратуру.
2.11.74. Операционный контроль термообработки, помимо мастера, осуществляют ИТР монтажного участка не реже одного раза в сутки на каждом посту.
2.11.75. У каждого стыка на расстоянии 100-150 мм от шва должно обозначаться несмываемой краской клеймо термиста рядом с клеймом сварщика.
При термической обработке сварных стыков трубопроводов должна записываться диаграмма автоматической регистрации температуры.
В диаграмму потенциометра ответственный термист-оператор заносит следующие сведения:
дату проведения термообработки сварного стыка;
наименование узла, привязки и номер стыка в соответствии с номерами точек на диаграмме;
скорость протяжки ленты самописца;
диаметр и толщину стенки трубы каждого стыка;
марку стали трубы;
фамилию, клеймо и подпись ответственного термиста;
вид нагревателя;
подпись мастера с грифом "принято".
2.11.76. При групповой термообработке на диаграмме должна производиться запись о том, какие стыки обрабатывались в группе с указанием типа нагревателя, характеристики теплоизоляции и на каких стыках измеряли и контролировали температуру.
2.11.77. По окончании смены мастер принимает от термиста диаграммы, подписывает их, сдает ответственному инженерно-техническому работнику, оформляющему документацию, который присваивает каждой диаграмме порядковый номер.
2.11.78. На основании диаграммы заполняется журнал термообработки и выписывается сертификат. Номер сертификата соответствует номеру диаграммы.
2.11.79. Журнал термообработки и диаграмма сохраняются на участке не менее 2 лет после сдачи объекта.
2.11.80. По окончании работ представляют сертификат термической обработки, список ответственных лиц с указанием должностей, список термистов с указанием их удостоверений, клейма, а также заключение об уровне твердости вместе с другой исполнительной документацией.